In polymer processing and material research, achieving uniform dispersion and distribution of additives and precise formulation control is crucial for developing advanced materials. This is achieved by a process called compounding.
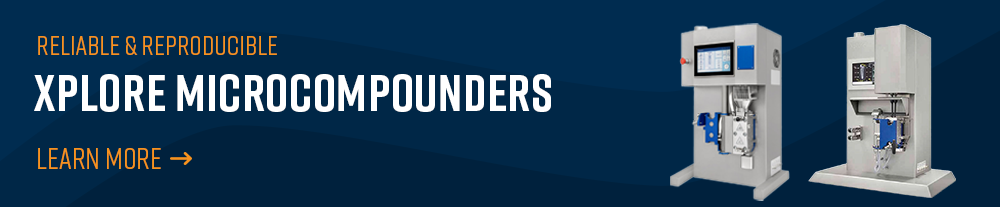
Microcompounding
Microcompounding is a small-scale polymer processing technique that involves mixing, blending, and modifying polymer materials using a specialized miniaturized instrument. It mimics the large-scale process but operates on a micro-scale. This process enables researchers and manufacturers to develop, test, and refine polymer formulations in small batches quickly, helping to conserve material and cost. Microcompounders allow researchers to speed up their polymer formulation development. It is ideal for material development, additive dispersion studies, and rapid prototyping before scaling up to full-scale production.
Microcompounder
A microcompounder is a miniature extruder designed for compounding small quantities of polymers with additives (Figure 1). Unlike conventional extruders used in large-scale industrial production, microcompounders typically operate with batch sizes of a few grams. They feature co-rotating or counter-rotating screws, a controlled temperature environment, and precise mixing capabilities, making them ideal for research applications. A microcompounder is ideal when developing compounds using expensive or rare materials and allows fine-tuning of shear, temperature, and mixing parameters. Microcompounders are also key for fast formulation development. Multiple samples can be formulated per day leading to significant decrease in the time required to develop a new formulation.
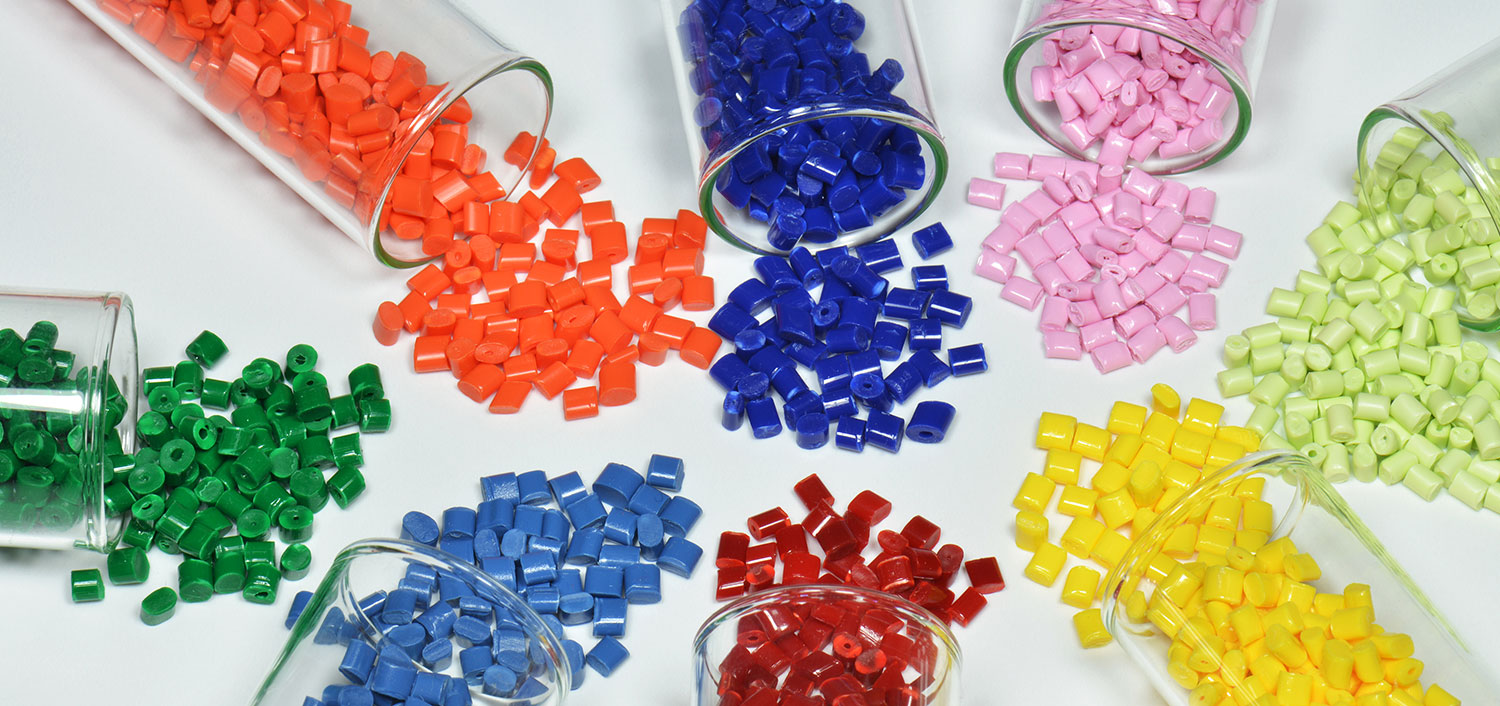
Advantages of a Microcompounder
Microcompounders simulate industrial processes and offer numerous advantages, particularly for research, process development and small-scale production environments including
- One of the biggest advantages of a microcompounder is its ability to process very small amounts of material. This is particularly useful when working with expensive or rare compounds, reducing material waste and cost.
- Microcompounders allow for quick iteration of different formulations, enabling researchers to screen multiple compositions efficiently before scaling up production.
- Microcompounders offer precise process control including temperature, shear, and mixing control that ensure materials are processed under optimal conditions, leading to reproducible and high-quality results.
- Although microcompounders are small-scale devices, they mimic industrial twin-screw extruders, making it easy to scale up successful formulations for commercial production.
- Microcompounders can be integrated with real-time analytics such as spectroscopy, rheology, and chromatography, providing immediate insights into material properties and process conditions. (For Xplore, this is a work in progress)
- Microcompounders are versatile instruments that support a wide range of polymer types and additives, from thermoplastics to elastomers and biodegradable materials, making them useful to different industries.
Applications for Microcompounding
Microcompounding finds applications in various industries, including polymer research, pharmaceuticals, and specialty materials development. Some of the primary applications include:
Polymer Research & Development
Microcompounding is instrumental in developing new formulations and optimizing material properties. Researchers can evaluate the effects of different fillers raging from micron to nanometer size, plasticizers, and reinforcements in small-scale experiments before moving to full-scale production. Reactive or non-reactive polymer blends can be optimized by testing various polymer combinations for improved mechanical, thermal, and chemical properties. Dispersion and efficiency of various additives such as fillers, flame retardants and stabilizers can be studied.
Pharmaceuticals
Microcompounding is used in the pharmaceutical industry for developing drug-loaded polymeric formulations.1 Drug stability and release can be investigated by incorporating the active pharmaceutical ingredients (APIs) in polymer matrices. Investigating new drug delivery mechanisms and development of personalized medicine is made feasible by microcompounding.
Electronics & Conductive Polymers
Microcompounding can be used in the development of conductive polymers where precise dispersion of conductive fillers like carbon nanotubes (CNTs) or graphene is critical. Electrically conductive polymers find applications in sensors and flexible and wearable electronics. On the flipside, developing lightweight composites for electromagnetic interference (EMI) shielding and high-performance polymers for heat dissipation are areas where microcompounding plays an equally important role.
Battery and Energy storage
Microcompounding plays an important role in battery research and development, particularly in the formulation and optimization of polymer-based electrolytes, conductive composites, and electrode materials. The ability to precisely control material composition and dispersion at a small scale makes microcompounders valuable for testing new battery materials before scaling up to industrial production. One of the major applications of microcompounding in battery research is the development of solid polymer electrolytes (SPEs), which are crucial for next-generation lithium-ion and lithium-metal batteries. Microcompounders can help with uniform dispersion of lithium salts within polymer matrices such as polyethylene oxide (PEO), polyvinylidene fluoride (PVDF), or polyacrylonitrile (PAN), and incorporation of nanofillers to enhance ionic conductivity and mechanical stability.
Medical Devices
Medical-grade polymers often require specific mechanical properties, sterilization resistance, and biocompatibility. Microcompounders can be used to develop controlled formulation and property enhancement of materials used in medical applications. Some examples include biocompatible polymer blends for use in prosthetics, implants, and medical tubing, antimicrobial polymer blends, bioresorbable polymers for temporary implants and sutures and specialized polymers for biocompatible 3D printing applications.
Biodegradable and Sustainable Materials
The growing demand for eco-friendly materials has resulted in microcompounders being widely used to develop biodegradable polymers and sustainable composites.2, 3 Researchers are developing alternatives to conventional plastics using biobased polymers like poly(lactic acid) (PLA) or polyhydroxyalkanoates (PHA); or natural polymers like starch or lignin and testing natural fiber reinforcements such as cellulose and hemp for sustainable applications.
Food Processing and Packaging
Microcompounders allow for efficient mixing and dispersion of functional ingredients into food matrices, ensuring homogeneous distribution and enhanced bioavailability.4 Enriching food films by blending vitamins, minerals and probiotics into edible films, encapsulating flavors and nutrients to protect them from degradation and developing time release flavor and nutrient formulations are some of the applications enabled by microcompounders. The food industry has utilized microcompounders to develop advanced food packaging materials with enhanced barrier properties and biodegradability. Oxygen and moisture barrier films improve the shelf life of packaged goods. Biodegradable packaging solutions are being investigated for compostable and edible packaging alternatives.
Advanced Composites
Microcompounders are playing a significant role in the development of high-performance (nano)composites for the aerospace, automotive, and defense industries.5 Lightweight composites are being developed with carbon or glass fibers for structural applications. High-temperature-resistant polymer blends are being developed for use in extreme environmental conditions. Protective gear and aerospace components are being developed using impact-resistant polymers.
Conclusion
Microcompounders are essential tools in polymer research, pharmaceuticals, biodegradable material development, electronics, medical device manufacturing, food packaging, and aerospace applications. Their ability to rapidly process small quantities of material with precise control makes them invaluable for formulation development and proof-of-concept studies before full-scale production. As material science continues to evolve, microcompounders continue to be a cornerstone of innovation in polymer processing and compounding.
References
- Stijn H.S. Koshari, S.H.S., Shi, X., Jiang, L., Chang, D., et.al. Design of PLGA-Based Drug Delivery Systems Using a Physically Based Sustained Release Model. Journal of Pharmaceutical Sciences 202. 111, 345 https://doi.org/10.1016/j.xphs.2021.09.007 ↩︎
- Acharjee, S.A., Gogoi, B., Bharali, P. et al. Recent trends in the development of Polyhydroxyalkanoates (PHAs) based biocomposites by blending with different bio-based polymers. J Polym Res 31, 98 (2024). https://doi.org/10.1007/ ↩︎
- Zarna C, Rodríguez-Fabià S, Echtermeyer AT, Chinga-Carrasco G. Influence of Compounding Parameters on the Tensile Properties and Fibre Dispersion of Injection-Molded Polylactic Acid and Thermomechanical Pulp Fibre Biocomposites. Polymers. 2022; 14(20):4432. https://doi.org/10.3390/polym14204432 ↩︎
- Mitacek, R.M., Ubbink, J., & Ismail, B.P. Improving functionality and texturization potential of novel pennycress (Thlaspi arvense) protein by inducing polymerization. Food Hydrocolloids 2024. 154, 110152. https://doi.org/10.1016/j.foodhyd.2024.110152 ↩︎
- Patel V, Joshi U, Joshi A, Oza AD, Prakash C, Linul E, Campilho RDSG, Kumar S, Saxena KK. Strength Evaluation of Functionalized MWCNT-Reinforced Polymer Nanocomposites Synthesized Using a 3D Mixing Approach. Materials. 2022; 15(20):7263. https://doi.org/10.3390/ma15207263 ↩︎