Nanofibers, with their high surface area-to-volume ratio, tunable porosity, and mechanical flexibility, are increasingly used in diverse applications including filtration, biomedical devices, energy storage, and smart textiles. Among the many fabrication techniques available, electrospinning and blow spinning have emerged as two of the most prominent methods for producing nanofibers from polymeric solutions. While both techniques can yield continuous nanofibers, they differ significantly in their operational principles, equipment requirements, scalability, fiber morphology, and suitability for different applications.
In this blog we compare electrospinning and blow spinning, outlining their mechanisms, strengths, limitations, and use cases to aid researchers and engineers in selecting the most appropriate method for their needs.
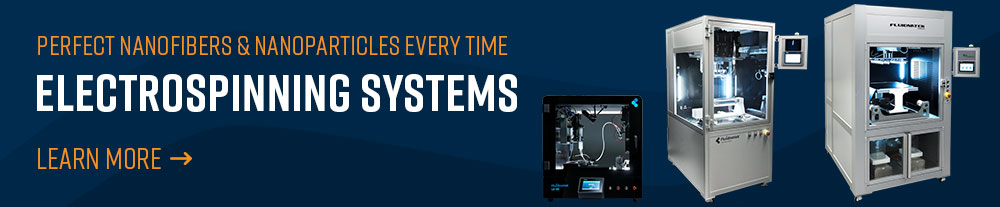
Fundamentals of Nanofiber Formation:
Nanofibers are typically formed by stretching a polymer solution into ultrafine threads that solidify via solvent evaporation. The success of this process depends on a delicate balance of viscosity, surface tension, and cohesive molecular forces within the polymer solution, as well as external forces that drive fiber formation. Electrospinning and blow spinning apply electric fields and high-velocity gas flow respectively, as the different driving forces to achieve nanofiber formation.
Feature | Electrospinning | Blow Spinning |
Driving Force | High-voltage electric field | Compressed gas flow |
Fiber Diameter | 20 nm – 10 µm (highly uniform) | 100 nm – 5 µm (variable, less uniform) |
Fiber Alignment | Good control and easy to fine-tune pore size | Poor alignment; mostly random deposition with uncontrolled pore size |
Material Versatility | Wide range, including complex composites, wide variety of solvents (regular solvents, ionic liquids and deep eutectic solvents) | Moderate; some polymers may not dry in time, limited in solvent selection |
Environmental Sensitivity | High (humidity and temperature affect output but are used to fine-tune sample morphology and microstructure) | Medium (temperature affects output) |
Collectors | Wide variety (flat plate, drum, mandrel, disk, roll-to-roll, liquid reservoir, among others) | Small variety (vacuum based collectors are preferred to minimize sample wastage) |
Electrospinning
Electrospinning uses electrostatic forces to draw charged polymer jets from a solution.1 A typical setup consists of a syringe containing the polymer solution, a high-voltage power supply (typically 1–50 kV), and a grounded or negatively charged collector (Figure 1a). When a voltage is applied, electrostatic repulsion overcomes the surface tension of the solution at the tip of the needle, forming a Taylor cone and ejecting a fine jet. As the jet travels toward the collector, the solvent evaporates, and the remaining polymer solidifies into fibers.
Electrospinning produces highly uniform fibers with diameters ranging from tens of nanometers to a few microns (Figure 2a). The user also has precise control over process parameters, such as voltage, flow rate, and tip-to-collector distance, that can be finely tuned for desired fiber morphology. Electrospinning can also be used to fabricate aligned fibers by using rotating drums as collectors. A wide range of polymers and composites can be electrospun, including bio-based and conductive materials.
Electrospinning is sensitive to humidity and temperature, and therefore an environmental control system is required to ensure jet stability, proper solvent evaporation rate, and fiber quality. Since electrospinning requires high voltages and possible use of toxic and flammable solvents, safety should be one of the considerations for electrospinning equipment.
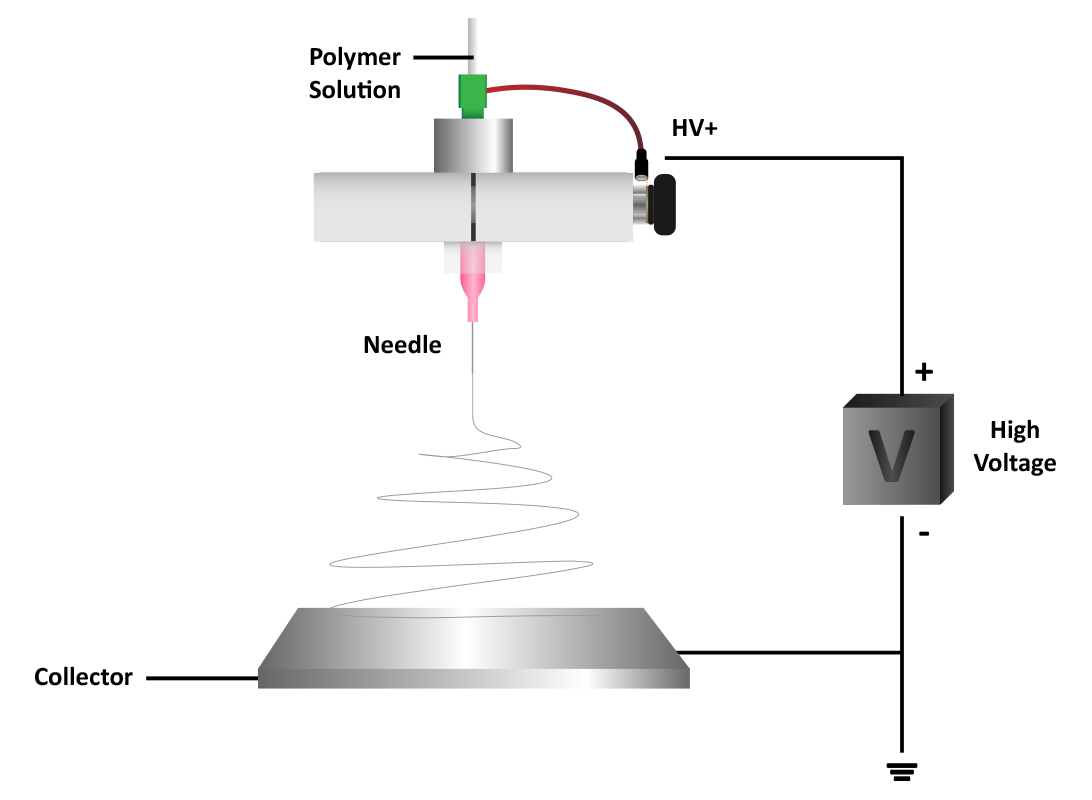
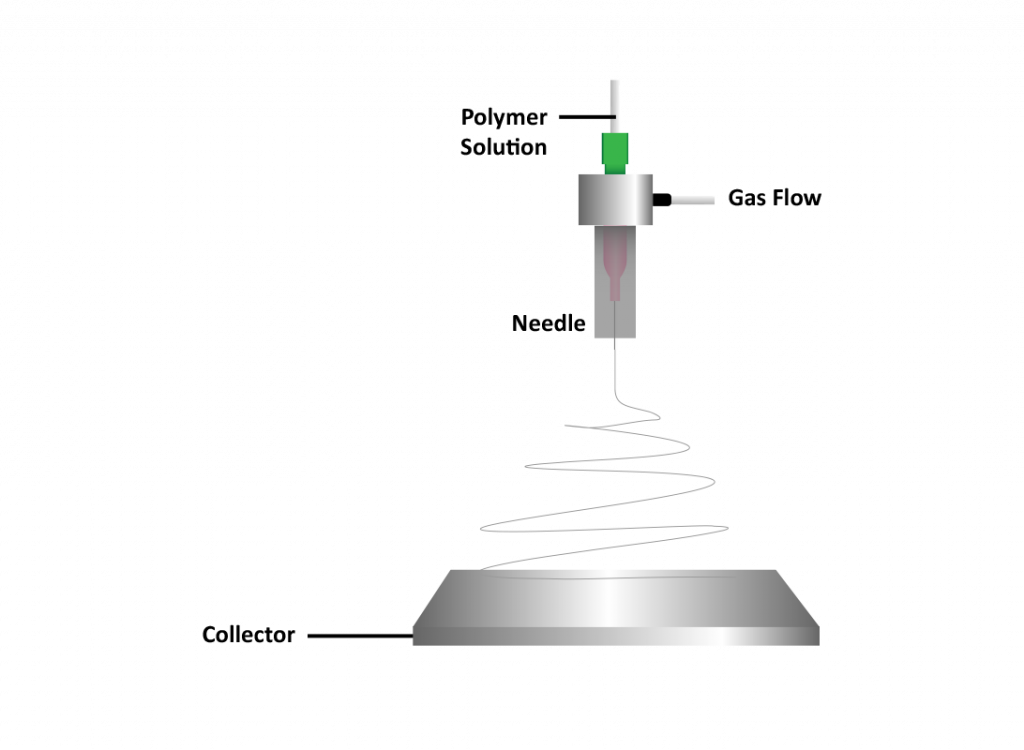
Blow Spinning
Blow spinning, also called solution blow spinning, utilizes a high-velocity gas stream (usually air or nitrogen) to elongate and dry a polymer solution into fibers (Figure 1b).2 As the gas impinges on the liquid, it stretches the polymer into thin fibers that solidify in-flight before reaching the collector. Typically, negative pressure is applied at the collector to properly collect the material, minimizing wastage.
Blow spinning can produce large quantities of fibers rapidly, making it attractive for industrial-scale manufacturing. However, blow-spun fibers are less consistent in their morphology and often have broader diameter distributions than electrospun fibers (Figure 2b). Achieving highly aligned or patterned fibers is challenging with the turbulent airflow involved in blow spinning. Also, the range of polymers that can be blown-spun is limited since the process works best with fast-drying solvents and relatively low-viscosity polymers.
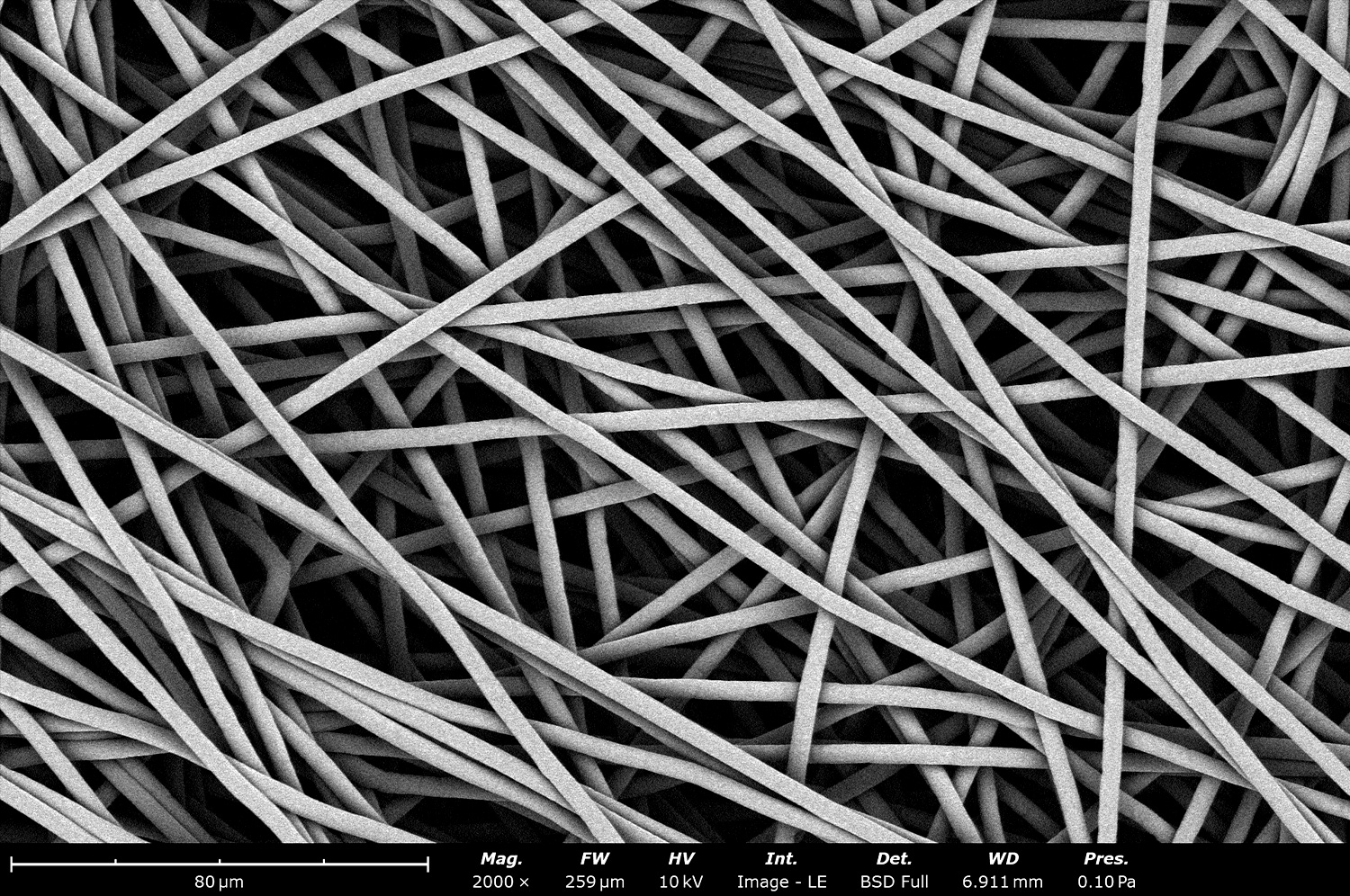
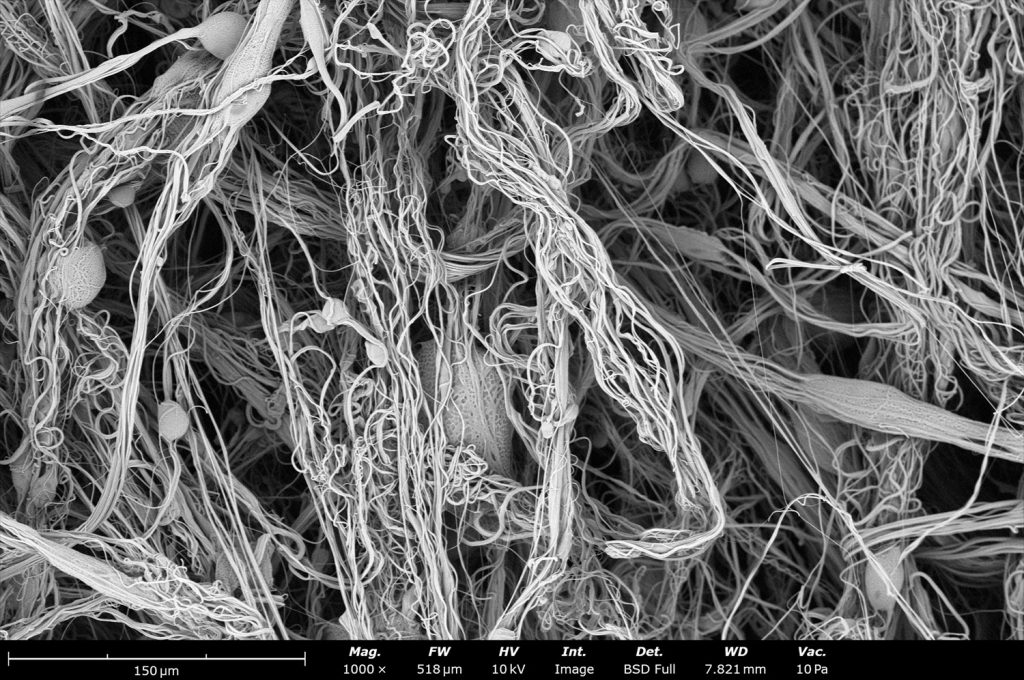
Applications:
Both techniques cater to different application demands based on fiber quality, volume, and processing environment. Electrospinning is ideal when highly uniform fibers are required. In biomedical engineering applications, electrospun scaffolds are widely used in tissue engineering, wound dressings, and drug delivery systems due to their uniform structure and ECM-like morphology. In energy storage, nanofiber electrodes for batteries and supercapacitors benefit from the fine structural control achievable via electrospinning. And in filtration applications dense electrospun mats are ideal for maximizing particle capture efficiency.
Although blow spinning is a more chaotic and less controlled process, it can be used in applications where large amounts of fiber are needed and the uniformity of the fibers is not critical. Blow-spun fibers can be sprayed onto large surfaces as protective coatings to fabricate hydrophobic or corrosion-resistant surfaces. In the fabrication of textiles and composites, blow spinning is used for high-throughput production of nanofiber mats for smart or wearable textiles.
Commercial systems:
The advantage for customers is that commercial systems, such as the Fluidnatek® line of electrospinning equipment, including the LE-50, LE-100, and LE-500, are designed to support multiple fiber fabrication techniques within a single platform (Figure 3). These systems can perform both electrospinning and solution blow spinning, offering flexibility for a wide range of materials and applications. Additionally, they support a hybrid mode known as electroblow spinning, which combines the electrostatic drawing forces of electrospinning with the mechanical elongation provided by high-velocity gas flow. This hybrid approach enables greater control over fiber morphology, enhanced throughput, and improved deposition on complex surfaces, making it ideal for research and scale-up environments where versatility and performance are critical.
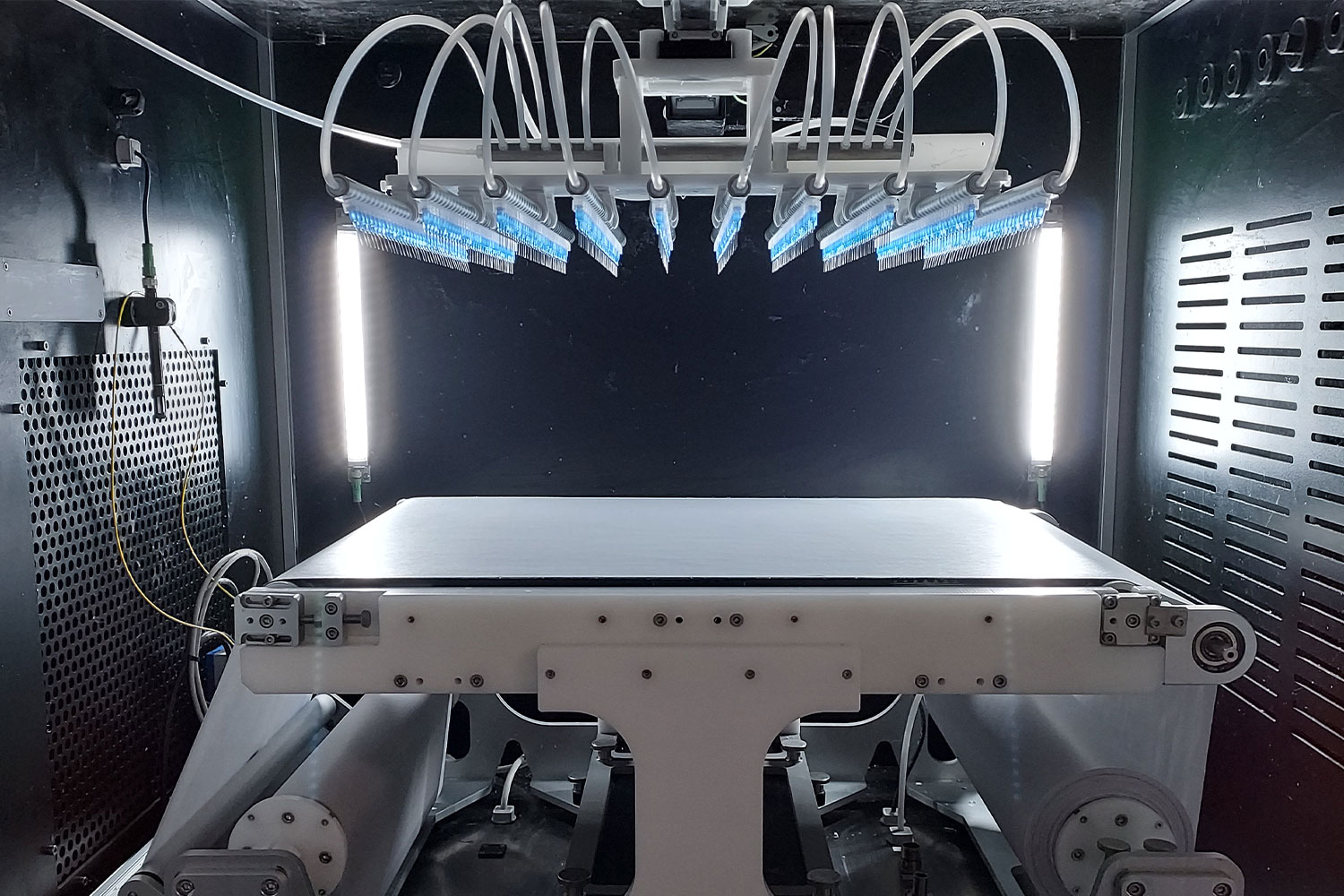
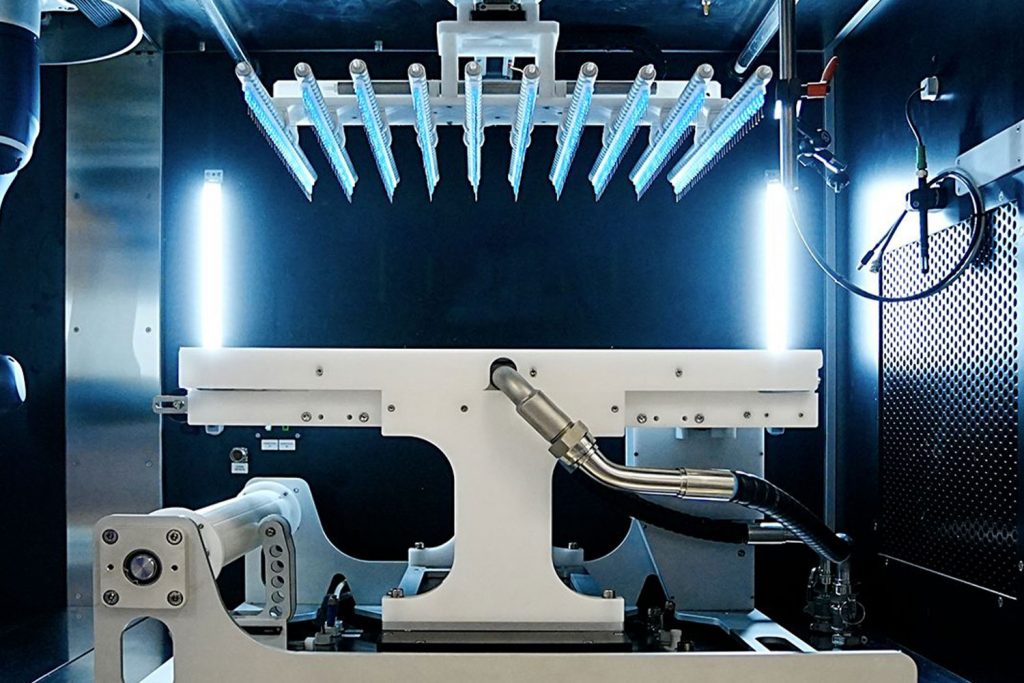
Conclusion
Electrospinning and blow spinning are complementary technologies for nanofiber fabrication, each with distinct advantages and limitations. Electrospinning offers exceptional control and fiber uniformity, making it ideal for high-performance applications. Blow spinning, in contrast, provides a scalable, cost-effective route to mass-produce nanofibers, particularly for coatings and textiles when fiber uniformity is not needed. The choice between these methods depends on application requirements such as throughput, fiber uniformity and/or orientation, and desired material properties.
References
- Bhardwaj, N.; Kundu, S. C. Electrospinning: A fascinating fiber fabrication technique. Biotechnology Advances 2010, 28 (3), 325–347. https://doi.org/10.1016/j.biotechadv.2010.01.004. ↩︎
- Daristotle, J. L.; Behrens, A. M.; Sandler, A. D.; Kofinas, P. A review of the fundamental principles and applications of solution blow spinning. ACS Applied Materials & Interfaces 2016, 8 (51), 34951–34963. https://doi.org/10.1021/acsami.6b12994. ↩︎