Nanofibers, or fibers with diameters on the scale of 10-9 meters, exhibit unique properties, differing significantly from the properties of the bulk materials. These include a large surface area to volume ratio, high porosity, high encapsulation efficiency, superior mechanical properties, and higher chemical stability. As a result of these remarkable properties, some versatile materials have found their way into a multitude of applications with the potential to address critical challenges in numerous fields and lead to a more sustainable and technologically advanced future.
As with any material, the process of scaling up production, to enable extensive use of nanofibers comes with issues like scalability, cost, and environmental concerns. Also, health and safety concerns and end-of-life considerations are critical to the widespread adoption of these amazing materials.
Challenges and Limitations
1. Scalability:
One of the primary challenges in nanofiber production is scaling up the manufacturing process to meet industrial demands. Many nanofiber fabrication methods are typically developed in laboratory settings and may not easily translate to large-scale production. Scaling up nanofiber production often involves addressing issues related to equipment design, process optimization, and ensuring consistent quality in mass production. To combat this, researchers and engineers are actively working on developing scalable nanofiber production techniques, such as needle-less electrospinning, multi-needle jet electrospinning, blow-spinning, melt-electrospinning, and melt-blowing to meet the requirements of various industries. There are a few industrial commercial products available that attempt to mitigate these limitations with instruments like the Fluidnatek HT that uses a multi-needle linear array to mass produce nanofibers at the industrial scale.
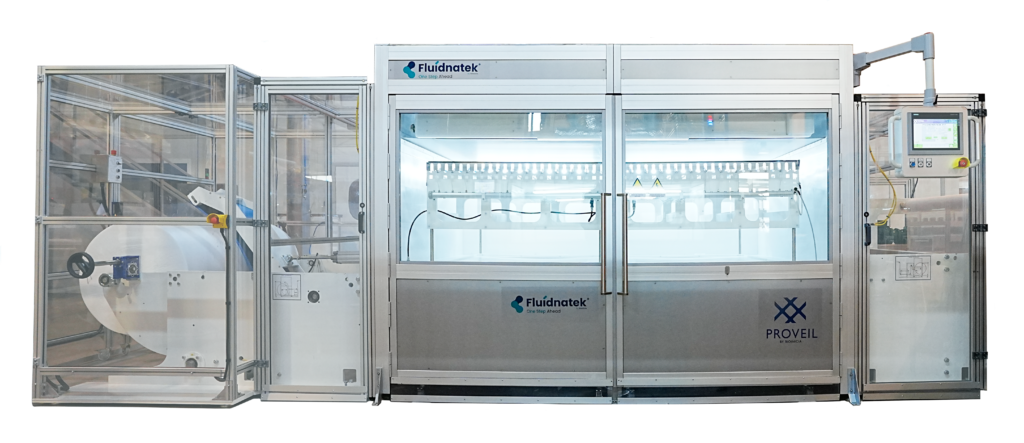
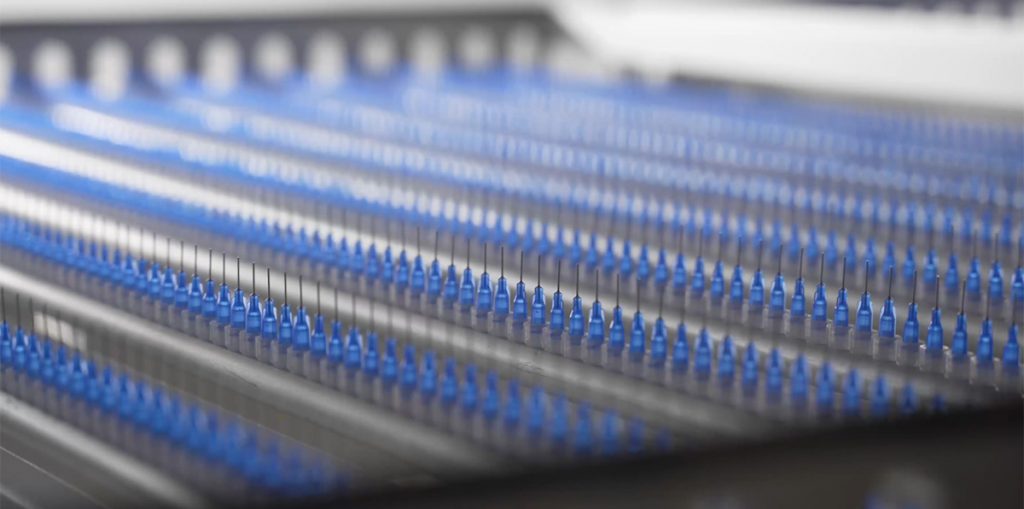
2. Cost:
While nanofiber production techniques can provide precise control of fiber diameters, wide usage of materials, and surface functionalization, they can be costly. This is primarily due to the use of specialized equipment, high energy consumption, and the expense of raw materials which can hinder the commercial viability of some nanofiber-based products. When considering how to reduce production costs, it may be difficult, yet critical, to maintain the quality and performance of the nanofibers. Therefore, efforts are being made to optimize production processes, develop cost-effective materials, and explore new production techniques that can lower the overall cost of nanofiber production. Some of these efforts include green electrospinning, scalable manufacturing, nanofiber and chemical recycling, and process automation, which aim to make nanofiber production more accessible and cost-effective, allowing for wider adoption and applicability across various industries. As technology matures, economies of scale will also contribute to cost reduction.
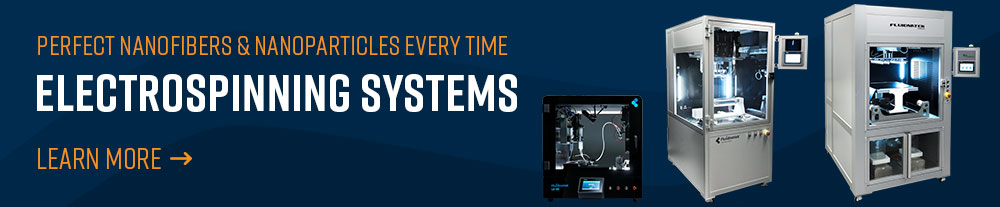
3. Environmental Concerns:
Environmental concerns, particularly related to waste and energy consumption, can also arise from nanofiber production and application. Nanofiber manufacturing processes could generate waste materials, including solvents and polymers, that may have environmental implications. However, recycling and waste management strategies are being developed to mitigate the environmental impact of nanofiber-based products. For example, one strategy to lessen solvent waste is to use a scrubber, which allows solvent to be recaptured during the production process followed by recycling and reuse. Polymers can also be recycled and reused based on the final application, e.g. the development of filtration media. Additionally, energy-intensive production methods may contribute to greenhouse gas emissions. To address these environmental concerns, researchers are exploring green and sustainable nanofiber production methods, like supercritical fluid processing or electrospinning, that minimize waste generation and energy consumption. As an example, carbon dioxide can be recaptured through different techniques like specialized filtration media or even converted to biodegradable polymers that can be processed for commercial products.
4. Health and Safety:
Nanofiber production and handling may pose health and safety risks to workers due to the inhalation of airborne nanofibers, exposure to potentially toxic materials, the use of hazardous chemicals during the production process, or exposure to other process byproducts. Ensuring the safety of workers and minimizing exposure to nanofiber-related hazards are critical concerns. Comprehensive health and safety protocols, including the use of appropriate personal protective equipment (PPE), proper ventilation systems, and adherence to official safety guidelines, are essential to mitigate risks associated with nanofiber production.
5. End-of-Life Considerations:
Finally, the disposal of nanofiber-based products at the end of their lifecycle can raise concerns about environmental impact and long-term sustainability. Like many emerging production methods or materials, developing strategies for the responsible disposal or recycling of nanofiber-based materials is an ongoing process. In the search for long-term solutions, researchers and industries are exploring biodegradable nanofiber materials and nanofiber recycling methods to address end-of-life considerations and reduce environmental footprint. For example, surgical masks can take many years to degrade in a natural environment. However, alternatives have been made with biodegradable polymeric filter media, like the biodegradable Proveil filtration mask, which can degrade naturally in less than 25 days.
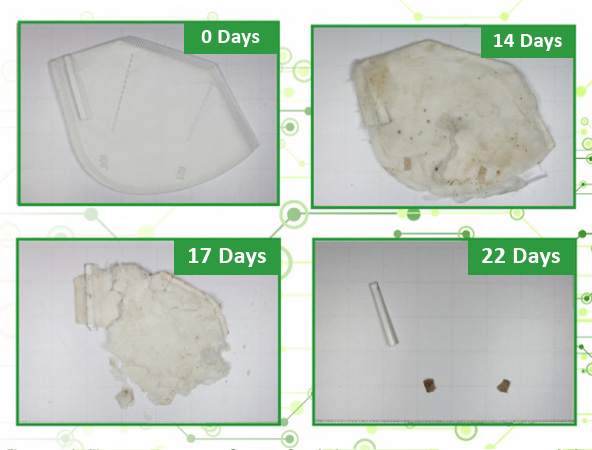
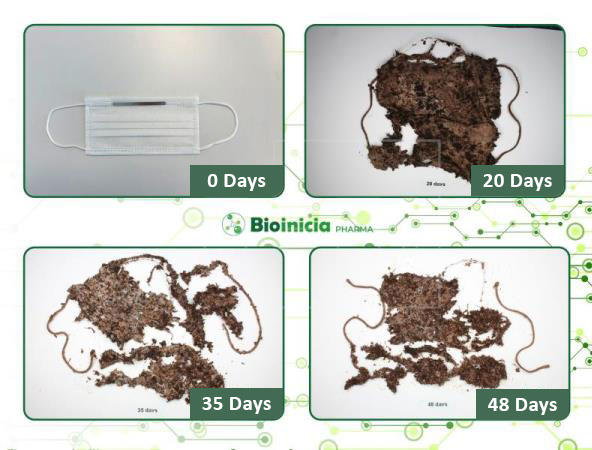
Conclusion
Increasing the usability of nanofibers is essential because it opens opportunities for innovation in healthcare, environmental sustainability, energy efficiency, advanced materials, and economic growth. Addressing scalability, cost, environmental, health, and safety challenges is crucial to unlocking the full potential of nanofiber technology and ensuring its responsible and sustainable integration into various industries. Ongoing research and innovation are key to finding solutions to these issues and advancing nanofiber technology.
Overall, the choice of the best way to make nanofibers depends on the specific material, properties, scale of production, and intended applications. Researchers and engineers often need to select the method that best aligns with their specific goals and constraints. Additionally, advancements in nanofiber production methods continue to evolve, offering new possibilities and improvements in nanofiber fabrication techniques.