What is Cross-Section Polishing?
In material science, cross-section polishing is a critical method to enable the detailed examination of a sample material’s microstructure. This technique is essential for understanding the composition, properties, and potential applications of various materials, from metals and ceramics to semiconductors and battery materials. By providing a pristine, flat, and highly reflective surface, cross-section polishing enables researchers and engineers to see inside the microscopic world of materials with precision and clarity.
Cross-sectional analysis requires a flat surface that exposes the inside of a material with as few artifacts as possible. To achieve this goal, a cross-section is polished in a way that removes material from the sample surface, eventually leading to a surface perpendicular to the original one. However, in some cases, materials are sliced at an angle in what is referred to as a ‘slope cut’ (30°, 60° for example). The goal, ultimately, is to achieve a cross-section that makes it possible to analyze features like layer thickness, interfaces, and possible defects, without interference from debris and distortions.
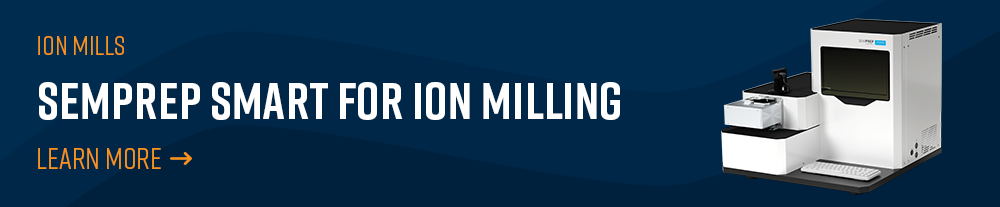
Why are Cross-Sections Polished?
Cross section polishing allows for the examination of internal structures without introducing artifacts that could distort the results. This process is crucial for:
- Failure Analysis: Identifying the root causes of material failure by examining fractures, corrosion, and other defects.
- Quality Control: Ensuring that materials meet specified standards and are free from internal defects.
- Research and Development: Innovating new materials and improving existing ones by understanding their internal composition and behavior.
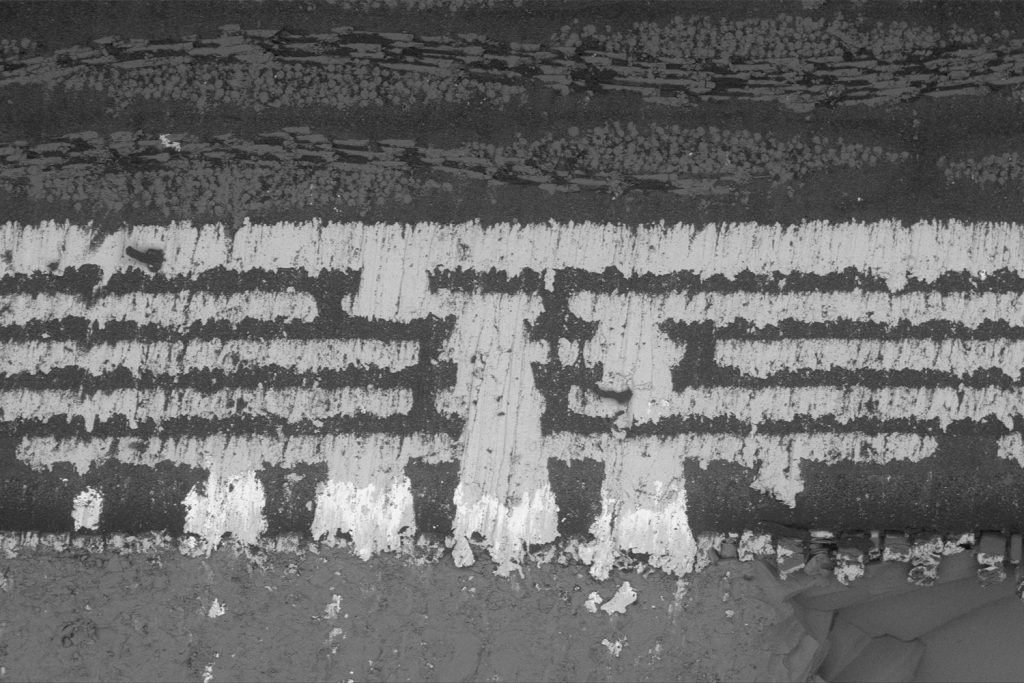
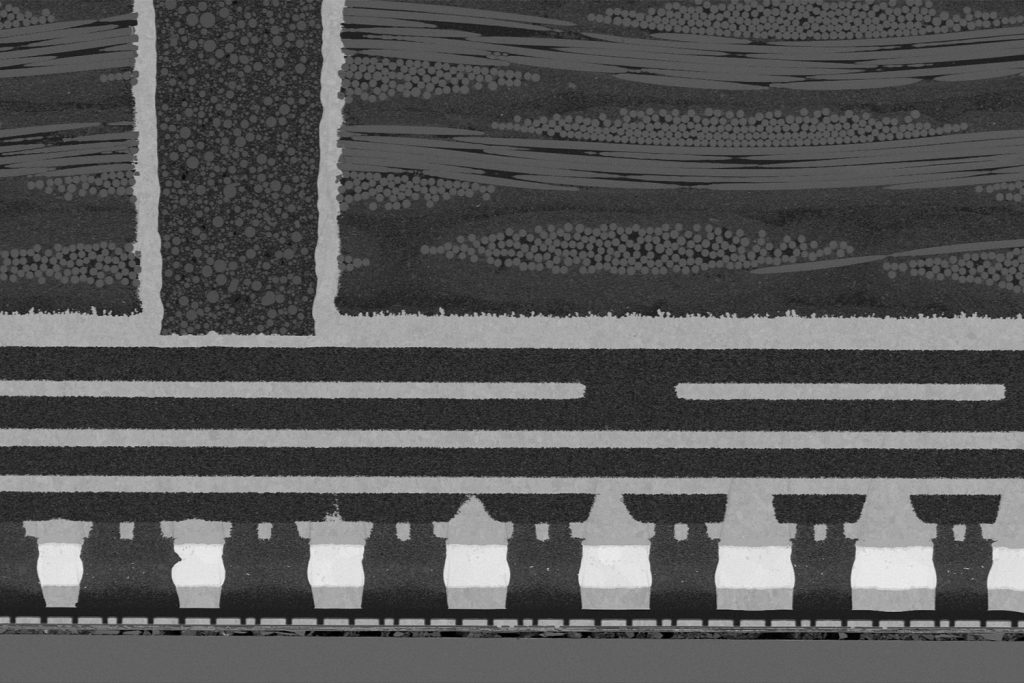
Process of Cross-Section Polishing
The cross-section polishing process typically involves several steps to achieve a high quality surface. The first step involves cutting or dicing the material to expose the area of interest. This is usually done using a precision saw to ensure a clean cut with minimal damage to the material; however, the initial surface will often be rough and uneven, and further preparations must be made for cleaner surfaces. Grinding is performed using abrasive papers or wheels of varying coarseness to achieve this relatively flat – albeit distorted – surface. The grinding process typically starts with coarse abrasives and progresses to finer ones. After grinding, the sample undergoes polishing with progressively finer abrasives, often down to sub-micron levels. This stage aims to remove the scratches or imperfections left from the grinding process. Diamond pastes, colloidal silica, or other polishing agents are commonly used. For applications that involve the study of microstructures in greater detail, ion milling should be the final step to achieve high quality surfaces. This technique uses a focused ion beam of argon to remove material at a very fine scale, providing an ultra-smooth surface ideal for high resolution imaging techniques.
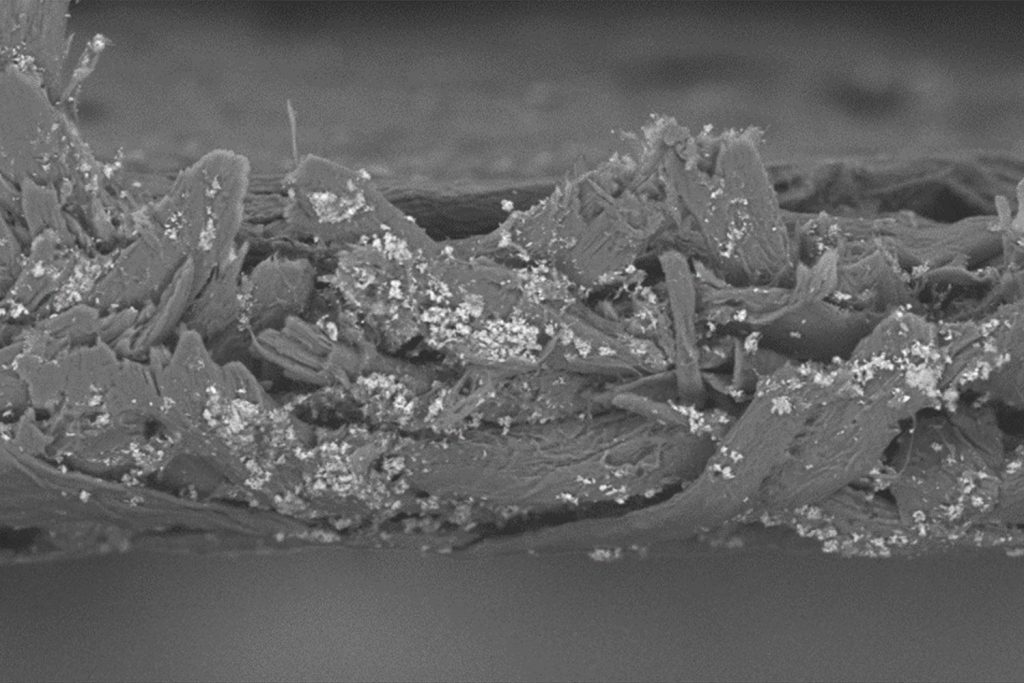

Ion Milling
Ion milling stands out among cross-section polishing methods due to its extreme level of precision and effectiveness. Unlike mechanical polishing, which can induce stress and mechanical deformation through shear forces, ion milling uses a beam of ions directed at the sample surface to remove material. This method is gentle yet powerful, enabling the removal of materials layer by layer without introducing physical distortions or artifacts that could compromise the integrity of a sample. Therefore, it is ideal as the last step in a polish process.
In Ion Milling, a beam of ions, typically argon, is accelerated towards the target material under vacuum. As the ions impact the surface, some of their energy is transferred to the sample and dislodge atoms from the surface, effectively milling it. This process allows for an extremely well controlled removal rate and depth, which is essential for achieving the high degree of surface finish required for microscopic analysis.
The Importance of ion beam Cross-Section Polishing
Smooth cross-section polishing with an ion beam is a critical component in ensuring the quality and accuracy of microscopic analysis. If the samples are only diced and mechanically polished, the images distorted and skewed, and the interpretation and accuracy of the data will be challenging. Two key reasons that distill the importance of ion beam cross-section polishing in scientific settings are as follows:
Enhancing Surface Quality for Microscopic Analysis:
A well-prepared, ion beam polished, cross-section provides a smooth, flat surface that is essential for high-resolution imaging with SEM and high-quality mapping using electron backscatter diffraction (EBSD) measurements 1 2. These polished surfaces reduce physical artifacts that can obscure or distort the image, thus allowing for clearer and more accurate observations of a material’s microstructure.
Improving the Accuracy of Material Characterization.
Material characterization often involves understanding the properties and behaviors of materials at a microscopic level, including phase distribution, grain boundaries, and defect structures. Cross-section polishing with ions ensures that these features are preserved and exposed with as minimal alterations as possible, facilitating precise measurements and analysis.
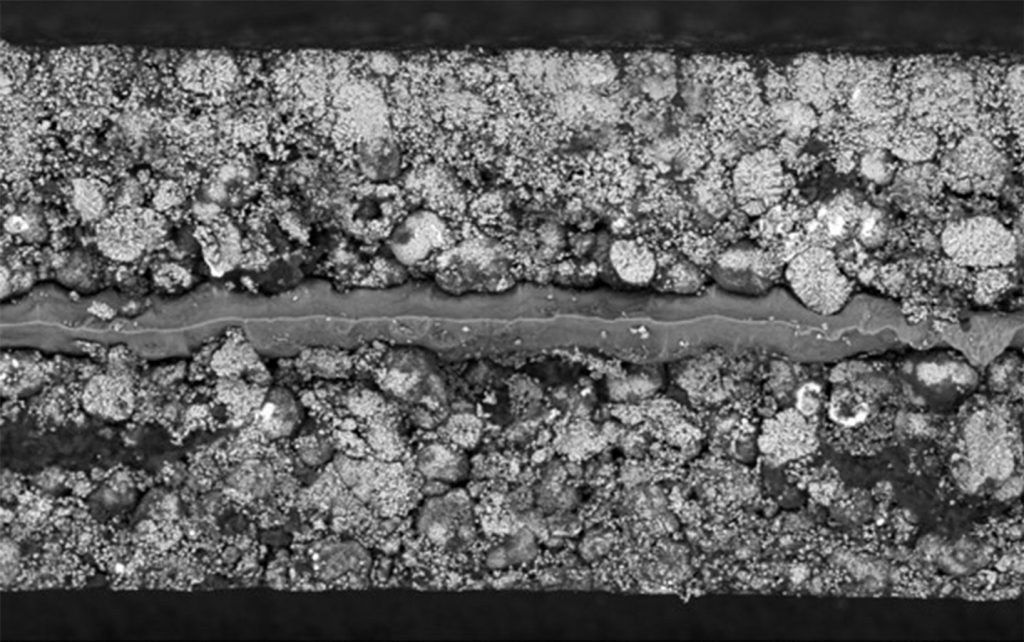
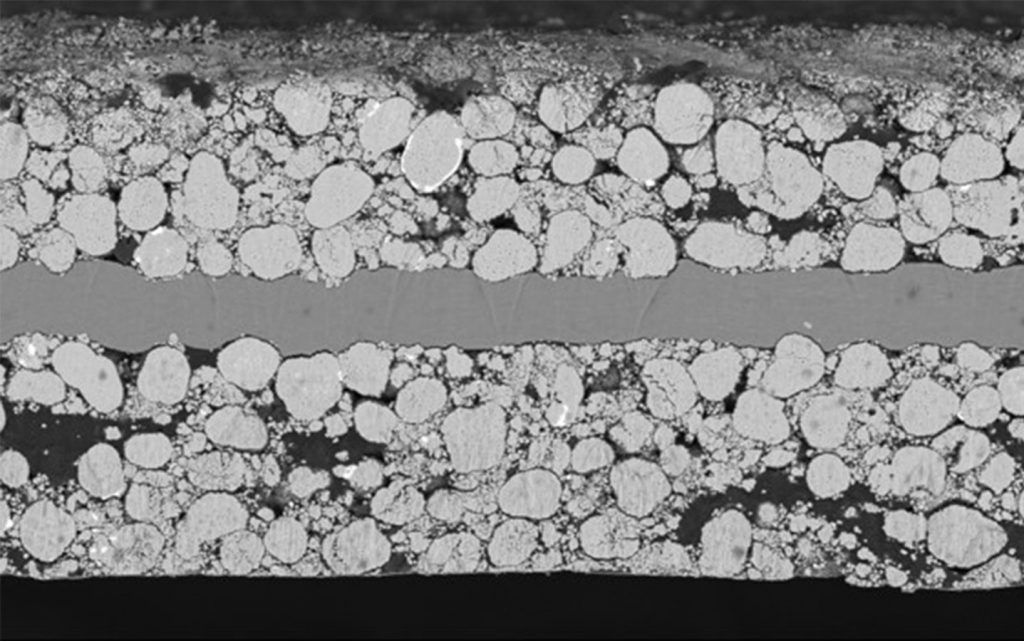
Applications of Cross-Section Polishing
Batteries and semiconductors:
Cross-section analysis is essential in the inspection of device architecture, layer interfaces, and defects during the fabrication and failure analysis of integrated circuits and microelectronic devices. Ion milling allows for the detailed study of interconnects, packaging, and microstructural features 3. In battery research, examination of electrode interfaces, material degradation, and failure mechanisms in battery materials are aided by ion milling.
Metallurgy:
Cross-section polishing is often used to investigate the internal structures of new composite materials and metals 4. This technique allows for a detailed analysis of phase distributions, inclusions, grain orientations, and the morphology of novel alloys and composites. Such insights are essential for developing materials with enhanced properties, such as increased strength, lightweight, or superior thermal resistance, which are vital for applications in aerospace, automotive, and construction industries.
Geology:
Geologists use cross-section polishing to study fine details relating to composition, structure, and history of minerals and rocks. Ion milling helps reveal the texture, composition, and succession of geological formations, providing clues about the sample’s history, mineral deposits, and environmental conditions at the time of it forming.
Biomaterials:
Cross-section polishing helps in studying the microstructure and compatibility of materials with biological tissues during the development of implants and prosthetics. Cross-sections of these materials can reveal insights into the internal morphology of these materials which are crucial parameters for optimizing their performance and functionality.
Conclusion
Cross-section polishing, especially when it includes the precise and gentle method of ion milling, plays a critical role in advancing our understanding and development of materials across many scientific and industrial fields. As this blog describes, the technique is highly valuable for revealing the subsurface features of various materials without artifacts—from the microelectronics in semiconductor devices to the complex phases in geological formations.
References
- Dankházi, Z., Kalácska, S., Baris, A., Varga, G., Radi, Z., & Havancsák, K. (2015). EBSD Sample Preparation: High Energy Ar Ion Milling. Materials Science Forum, 812, 309–314. https://doi.org/10.4028/www.scientific.net/msf.812.309 ↩︎
- Glenn, A. M., Liu, W., MacRae, C. M., Wilson, N. C., & Torpy, A. (08 2022). An EBSD – EPMA Investigation of Synthetically Produced Sulfide Ores. Microscopy and Microanalysis, 28(S1), 642–644. doi:10.1017/S1431927622003087 ↩︎
- Madec, L., Ledeuil, J.-B., Morey, J., & Martinez, H. (2023). Cross-section nano-Auger/SEM analysis to reveal bulk chemical/morphological properties of composites for energy storage. Electrochimica Acta, 448, 142185. doi:10.1016/j.electacta. 2023.142185 ↩︎
- Bondareva, O.S., Dobychina, O.S., Melnikov, A.A. et al. EDS + EBSD Phase Analysis of the Zinc Coating Formed on Steel in a Melt with Nickel Microadditives. J. Surf. Investig. 16, 1069–1073 (2022). https://doi.org/10.1134/S1027451022060064 ↩︎