Introduction
Technical cleanliness is the exhaustive control of contamination across manufacturing and assembly of components to protect product integrity. In precision systems, undesirable particles can be detrimental to functionality, eroding and abrading surfaces through repetitive contact (Figure 1). Trapped between tight fits, they essentially act as microscopic sandpaper between components – or in some cases – stress concentration points that introduce cracks and fractures. In other cases, conductive particles short-circuit electronic pathways by bridging metal traces and power sources. Unwanted contamination can originate internally (e.g., wear and tear debris) or externally (e.g., environmental particles introduced by production tools and ambient air, including particulates of steel, brass, SiO2, and aluminosilicates). These relentless microscopic threats exist across every industry where precision matters.
In automotive manufacturing, abrasive dust particulates can infiltrate engines to heighten the wear of tight mechanical fits through repetitive contact. Small particulates can also clog and obstruct narrow hydraulic lines and nozzles, resulting in failure of critical hydraulic systems like brakes and power steering. Additionally, a single conductive particle entering sensitive electrical components like sensors or engine control units can bridge circuits and trigger electrical shorts. Microelectronics are further susceptible to product-killing nanoscale contaminants that may evade traditional detection methods yet catastrophically burn out integrated circuit traces once activated. In implantable medical devices, trace biological or inorganic contaminants risk triggering severe inflammatory responses in patients.
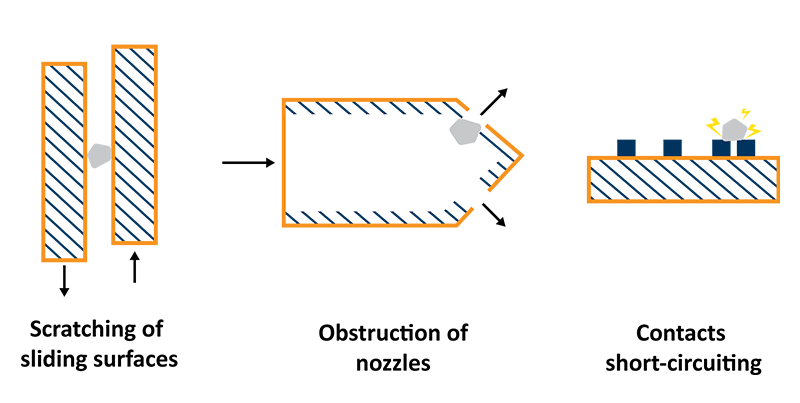
With advancing technologies across sectors, cleanliness standards continue intensifying while maximum allowable particle sizes shrink. Maintaining exceptional technical cleanliness is increasingly essential to managing risk, ensuring proper function, safety, and avoiding failures over long service life.
Techniques for Monitoring Technical Cleanliness
First-line methods for basic cleanliness monitoring including gravimetric analysis, particle counters, and optical microscopy remain useful but have inherent limitations that restrict their usefulness in solving cleanliness issues. All these techniques involve using an appropriate solvent to flush the system or component. The particles in the solvent can be directly characterized using a particle counter. However, for gravimetric analysis and optical microscopy, the solvent is then run through a filter and the particles captured on the filter are characterized.
Gravimetric analysis is a mass-based technique to gauge overall contamination levels. The filter is carefully weighed before and after collecting the particles using a precision microbalance. The difference in mass represents the total contaminant. While straightforward, this bulk measurement provides no insights into particle size distribution, morphology, or composition, and therefore potential sources cannot be determined. It simply quantifies the total accumulation, which could range from a few large particles to millions of nanoscale contaminants. To fully characterize the contaminants, more advanced analytical methods are required.
Particle counters serve as workhorse instruments for monitoring particle populations in real-time. A controlled volume of air or fluid is continuously drawn in and then passed through a laser beam focused across the flow path. As particles intersect the beam, they scatter light proportional to their size. This scattering of light is measured by a photodetector and associated with a particle size range. Size binning allows the construction of a particle-size histogram by counting particles in each range over time. While common for cleanroom monitoring, particle counters are blind to sub-micron contaminants below the sensitivity limits and are not able to sufficiently characterize particle morphology or composition for root cause analysis.
Workflows with optical microscopy involve imaging the filters with the particles under high magnification. A combination of a motorized sample stage and camera makes it possible to automate the screening process. Automated software classifies particulates based on metrics like size and edge sharpness, but the diffraction limit of visible light restricts resolution to particles only about 2 μm in diameter or larger. It also provides no information on composition.
The restricted ability of these methods to provide morphological and compositional information reveals very little or nothing about particulate shape, size, structure, or material makeup. Without such data, identifying the root cause of contaminants becomes a matter of guesswork. For example, ambiguous metallic particulates observed in an optical microscope may originate from machining, wear, or environmental ingress. Lacking critical details about morphology and composition, issues could go uncorrected for a long period.
Scanning Electron Microscopy
Scanning electron microscopy (SEM) grants comprehensive insights far beyond conventional methods. SEM offers advanced characterization at high resolution, providing improved size sensitivity and analytical capabilities by benefiting from synergy with energy-dispersive X-ray spectroscopy (EDS). The electron beam of an SEM raster scans across the sample surface and can routinely resolve details less than tens of nanometers in size – over a million times finer than the human eye. In addition, the characteristic X-rays originating from unique elements in the sample are detected through EDS to identify the composition of individual particles. Together, the high magnification, resolution, and integrated compositional characterization make SEM/EDS an incredibly powerful tool for cleanliness analysis. The advantage of SEM over traditional methods allows a deeper understanding of microscopic contamination for better quality and process control.
Though SEM offers immense analytical power, conventional implementations present some barriers to production-scale cleanliness monitoring. Many facilities choose to outsource SEM analysis to external labs. This can introduce long lead times and additional contamination as samples are prepared, packaged, and shipped over days. Further inconsistencies arise as manual handling can introduce issues in sample preparation, instrument configurations, and operator skills. To ensure reliable and timely data, extensive coordination is required to manage external partners.
The ideal scenario for cleanliness monitoring via SEM/EDS is to obtain an in-house system to ensure real-time monitoring with consistent protocols. Recent engineering breakthroughs have resulted in compact and intuitive desktop SEM systems, ideal for use in industrial environments. By providing instant results, contamination issues can be corrected as they arise, rather than waiting days for outside analysis to yield insights. Production yield is maintained when cleanliness obstacles are swiftly identified and eliminated through closed-loop, in-house SEM monitoring.
One pioneering system leading the way to harness the power of an automated in-house SEM/EDS as a dedicated industrial cleanliness analysis tool is the Phenom ParticleX Technical Cleanliness (ParticleX TC) Desktop SEM. ParticleX TC integrates advanced SEM technology with streamlined sample handling and intuitive software in a compact desktop footprint. Built on the Phenom XL Desktop SEM, it uses a long-lifetime, high-brightness cerium hexaboride (CeB6) electron source that provides a high signal-to-noise ratio and requires minimal maintenance. Automation is accomplished with Perception, a separate UI dedicated to automated SEM tasks (Figure 2).
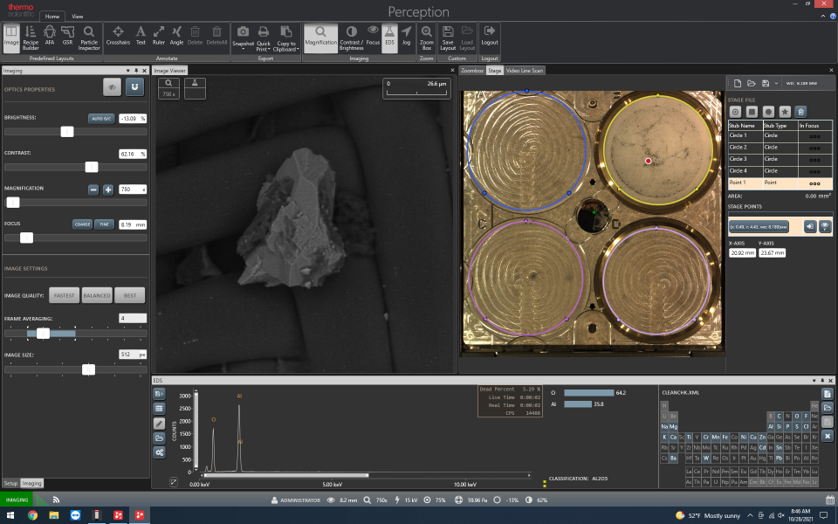
Key capabilities include high-resolution imaging capable of detecting particles as small as 20 nm and extensive analysis of said particles including size and morphology measurements, compositional classification through EDS, and flexible, standard-compliant reporting.
Automated reporting of hardness based on EDS data provides further insights regarding the impact of particulate contamination to aid in decision making. Hardness classification rules can contain rounded hardness values (e.g., hard, medium, and soft), allowing particles to be sorted and displayed with colors in the report as well to indicate their hardness rating (Figure 3). Custom cleanliness rules allow maximum particle counts to be set for each classification rule based on hardness or other properties for actionable pass-fail reporting.
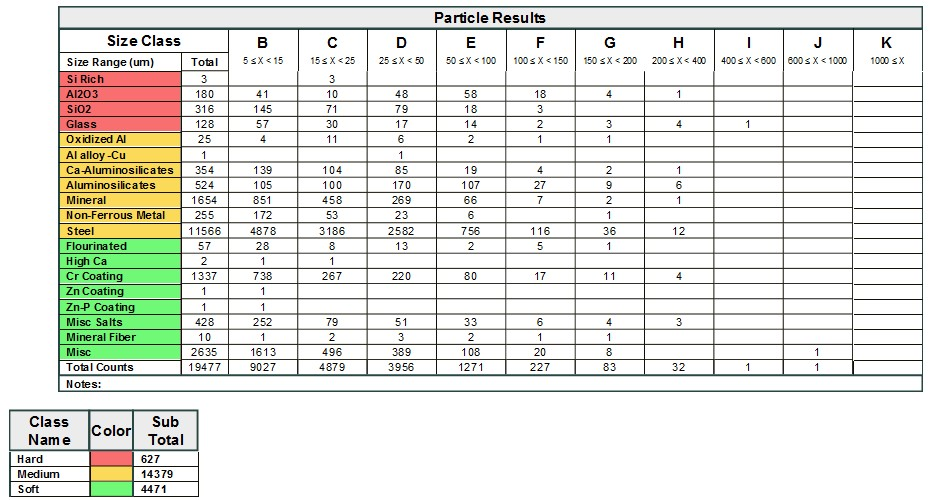
With minimal training required, the instrument can be readily deployed on the production floor within a short time frame. This system exemplifies how purpose-built, on-site SEM can provide a variety of manufacturing industries with unprecedented insights into micro to nanoscale surface properties – critical for thorough quality control and continuous improvement.
Automotive Manufacturing
ParticleX TC enables rapid root cause analysis of particles and contaminants in automotive engines and other precision components. Once components are washed and particles filtered, ParticleX TC enables in-depth analysis of collected contaminants (Figure 4). Quantitative morphological measurements and composition classification can differentiate between aluminum originating from machining operations and jagged chromium flakes generated by gear wear, for example. By tracing these intrinsic particles back to their specific sources, targeted process improvements can be implemented to reduce the particulates most prone to wear damage over time. The system also can help identify sources of extrinsic debris before they can accumulate to catastrophic levels. Its sensitivity meets stringent automotive cleanliness standards for microscale particles, enabling routine verification testing during production and intervention when thresholds are exceeded.
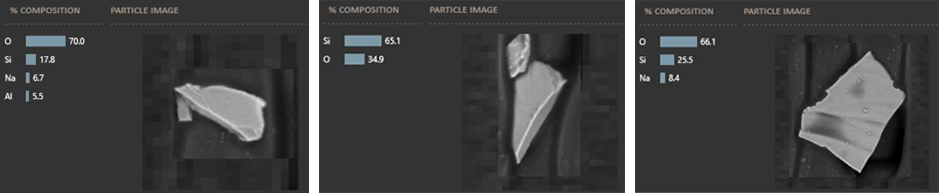
The ISO16232 and VDA-19 standards exist to provide consistent technical cleanliness control in automotive manufacturing worldwide. These rigorous cleanliness standards outline test methods, sampling techniques, particulate extraction procedures, and analysis methods to precisely quantify cleanliness levels on components. Standardizing this process enables objective, comparable cleanliness assessment across global supply chains.
Adhering to ISO16232 and VDA-19 is imperative for automotive component suppliers and manufacturers because particle contamination can critically undermine performance and reliability. Even miniscule particulates left unchecked can lead to reduced efficiency, increased wear, and outright system failures. These standards provide assurance that cleanliness is controlled through the supply chain, giving suppliers clear requirements to fulfill and manufacturers confidence in received components.
This is where automated SEM systems provide critical value. Once components are washed and particles filtered, ParticleX TC enables in-depth analysis of collected contaminants. Imaging reveals particulate size of morphology distributions, while integrated EDS identifies compositions indicative of process contaminants. This particle evidence is vital for remedying contamination sources and preventing future defects.
ParticleX TC outputs standard-compliant reports documenting particle populations by composition, size range, cleanliness level, and straightforward pass-fail results per ISO16232/VDA-19 guidelines (Figure 5). Its automated analysis capabilities let the system run continuously overnight, eliminating outsourcing delays for fast, actionable cleanliness insights. Pairing optimized, disciplined extraction procedures per the standards with thorough SEM particulate characterization and reporting gives manufacturers and suppliers optimal technical cleanliness control.
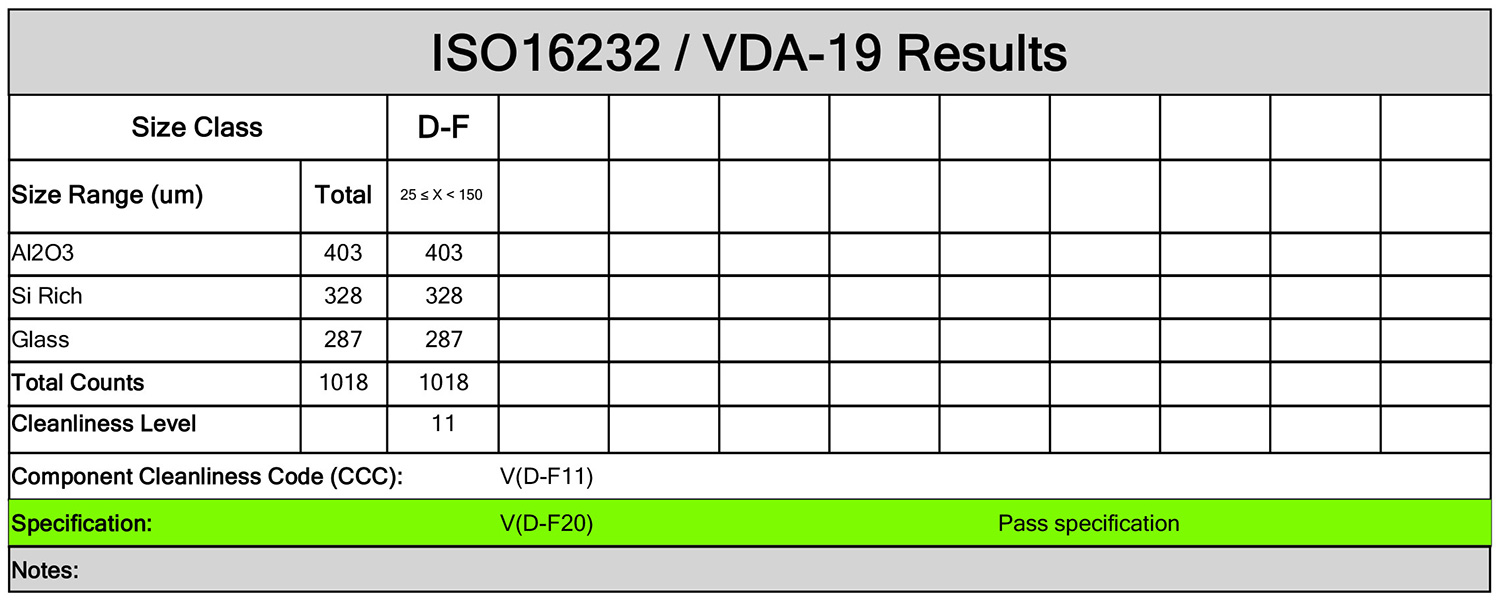
Aerospace
In aerospace, technical cleanliness is imperative for unwavering flight safety and performance. Engines contain intricate turbine blades with microscopic clearances where stray particulates pose a threat to accelerate wear and affect thrust if left untouched. Particulates also disrupt thermal regulation in engines, creating dangerous hot spots. Hydraulic systems like flight controls and landing gear operate with extremely low tolerance for contamination – a particle obstructing a narrow hydraulic line or nozzle can cause complete failure of critical systems. Furthermore, a sole stray conductive particle entering electrical wiring or sensitive avionics components can bridge circuits and trigger electrical shorts that lead to control and navigation system failure.
With such dire consequences, aerospace technical cleanliness standards are extremely rigorous throughout component manufacturing and vehicle assembly. Parts undergo extensive precision washing and packaging in order to adhere to the various standards set in place. Robust process monitoring and testing verifies ongoing cleanliness down to nanoscale levels, quantifying particulate sizes, concentrations, and chemistries – all of which are capabilities enabled by ParticleX TC.
Electronics
Technical cleanliness is important in electronics manufacturing as devices become more miniaturized and sensitive. Contamination particles as minute as 10 nm can cause catastrophic failures once products are operational. For example, nanoscale debris lodged in integrated circuits can bridge contacts causing electrical shorts. These microscopic, short circuits lead to immediate or intermittent device failures. Conductive particles also lower insulating resistance, creating leakage currents that disrupt digital signals. Moreover, contaminant particles obstruct the proper wetting of adhesives and solder onto component leads, attenuating the bonding strength and disrupting the electrical conductivity critical to electronics functionality. And of course, as circuits shrink in size, unwanted abrasive particles become ever more detrimental.
With resolution down to tens of nanometers, the imaging of ParticleX TC visually identifies problematic particulates across samples while integrated elemental analysis of the system via EDS reveals chemical compositions to trace contamination sources, helping to improve production and assembly processes by targeting the most devastating contaminant types found in electronics manufacturing.
Medical Devices
For medical devices destined to reside in the human body, stringent cleanliness standards are vital to minimize safety risks. Contaminants left behind during manufacturing, handling, or packaging can spell disaster once implanted. For instance, microscopic debris or chemical residues left on the surface of a device could trigger inflammatory responses, provide anchor points for dangerous biofilms, or abrade and induce overall failure. Thorough contaminant testing and control is thus essential to ensure device safety and performance.
Modern automated imaging solutions such as ParticleX TC combine electron microscopy, EDS, and automatic workflows to extract rich data on sizes, distributions, morphologies, and chemistries of surface particulates. Reporting can be customized to deduce contamination pathways with the aim of elevating patient protection.
Summary
Strict control of technical cleanliness is essential for quality and safety across manufacturing industries. By enabling high-throughput technical cleanliness monitoring, the ParticleX TC Desktop SEM provides actionable data leading to real-time decision-making on the production floor. This enables proactive quality improvement through detecting, visualizing, and classifying microscopic particulates. With automated SEM imaging and microanalysis, issues can be identified earlier, and corrective actions implemented faster. With Phenom’s vigilant eye on production processes, manufacturers can preemptively cure cleanliness concerns before products leave the door.