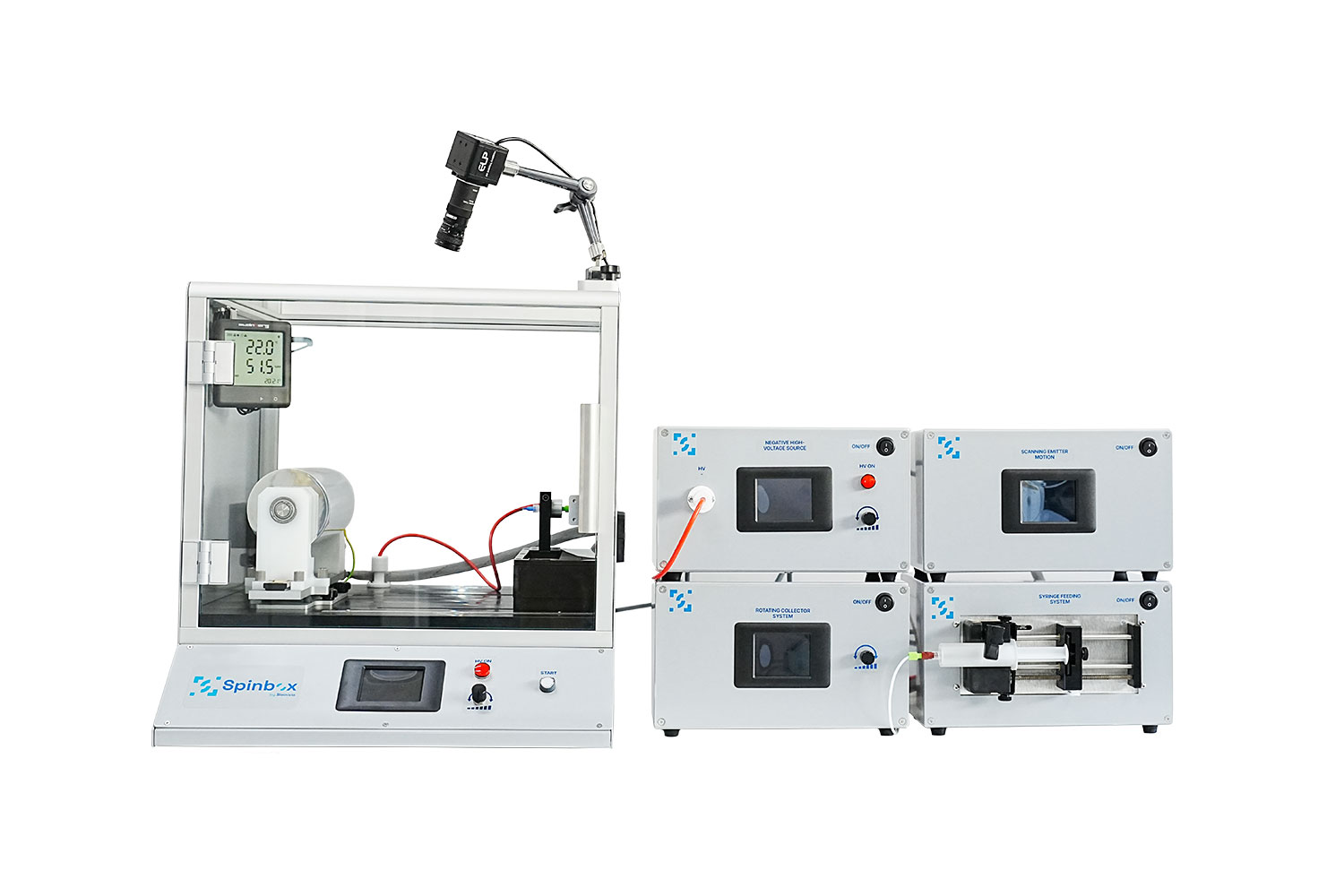
Spinbox® Electrospinning & Electrospraying System
Spinbox®
Ideal for proof-of-concept of new materials and formulations. Its wide range of capabilities and exceptional reliability allows scientists to efficiently prototype and optimize their concepts.
Research-Grade Capabilities
Control 7+ parameters for nanofiber or nanoparticle development.
Compact & Ergonomic Design
Designed to fit in small laboratory spaces with built-in critical safety features.
Talk to an Instrumentation Specialist Today!
Benchtop Electrospinning system designed for small lab spaces
The Spinbox not only offers the basic essentials to create electrosprayed particles and electrospun fibers, but it also offers a chemically resistant cabinet and multiple features to obtain aligned fibers, core-shell particles or fibers, ability to increase uniformity and production, among many other capabilities. As compared to home-built systems, this unit also offers the advantage of a passive exhaust system to remove gas solvents from both processes allowing the user to maximize their fume hood workspace. With the capability to work in horizontal or vertical spinning configurations, this unit offers flexibility for all of your application needs.
Application Areas:
Spinbox®
Product Features
Standard Product Features
The Spinbox system supports small-scale production, making it ideal for concept development. It features modular control, allowing users greater flexibility in operation. The standard high voltage power supply has an adjustable range from 0 to +30 kV, and the system has a safety shut-off switch integrated directly into the access doors for added protection. Solutions can be dispensed using either syringe pumps or pressurized vessels and the target distance can be adjusted manually from the emitter to the collector. The Spinbox also features a passive exhaust system is used to manage airflow and remove fumes effectively.
Optional Upgradeable Features
Some optional upgrades include an adjustable negative high voltage power supply, ranging from -10 to 0 kV, which can enhance sample deposition control. The spinbox can be expanded to support up to three syringe pumps, allowing for coaxial or triaxial processing configurations to meet advanced material requirements. A Taylor cone visualization system can enable real-time monitoring of the electrospinning process for improved accuracy and consistency. Additionally, a scanning emitter motion is used to improve the uniformity of thickness distribution across the target surface. Lastly, the rotating collector can be configured with a disk, drum, or mandrel, providing versatility in sample collection.
Kit Configurations
Basic Spinbox Kit
Enter the world of professional electrospinning and electrospraying instruments with this easy-to-use kit that prioritizes reliability and safety.
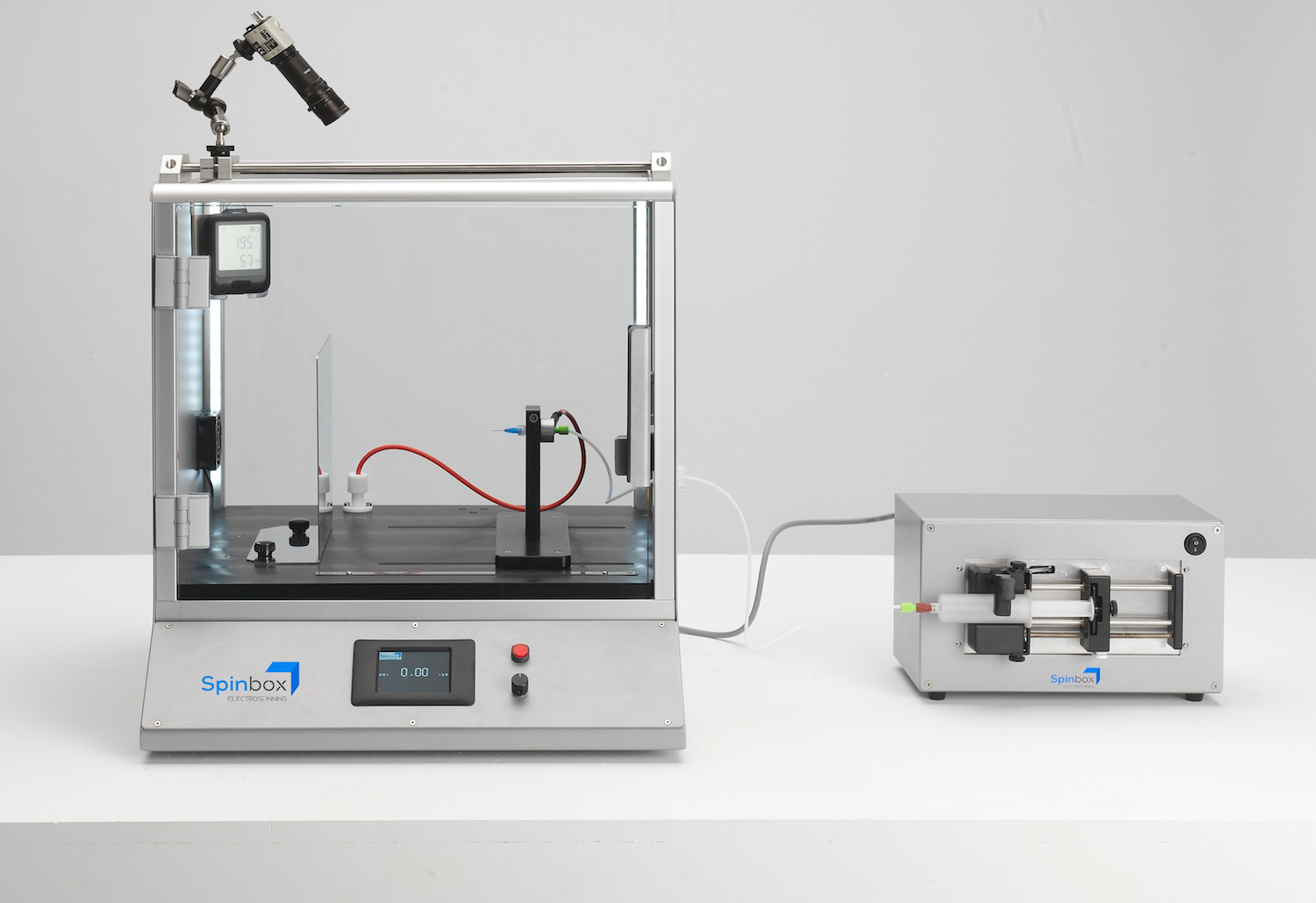
Intermediate Spinbox Kit
All the benefits of the Basic Kit, plus a rotating drum collector system for generating aligned fibers. Updateable at any point with plug-and-play accessories.
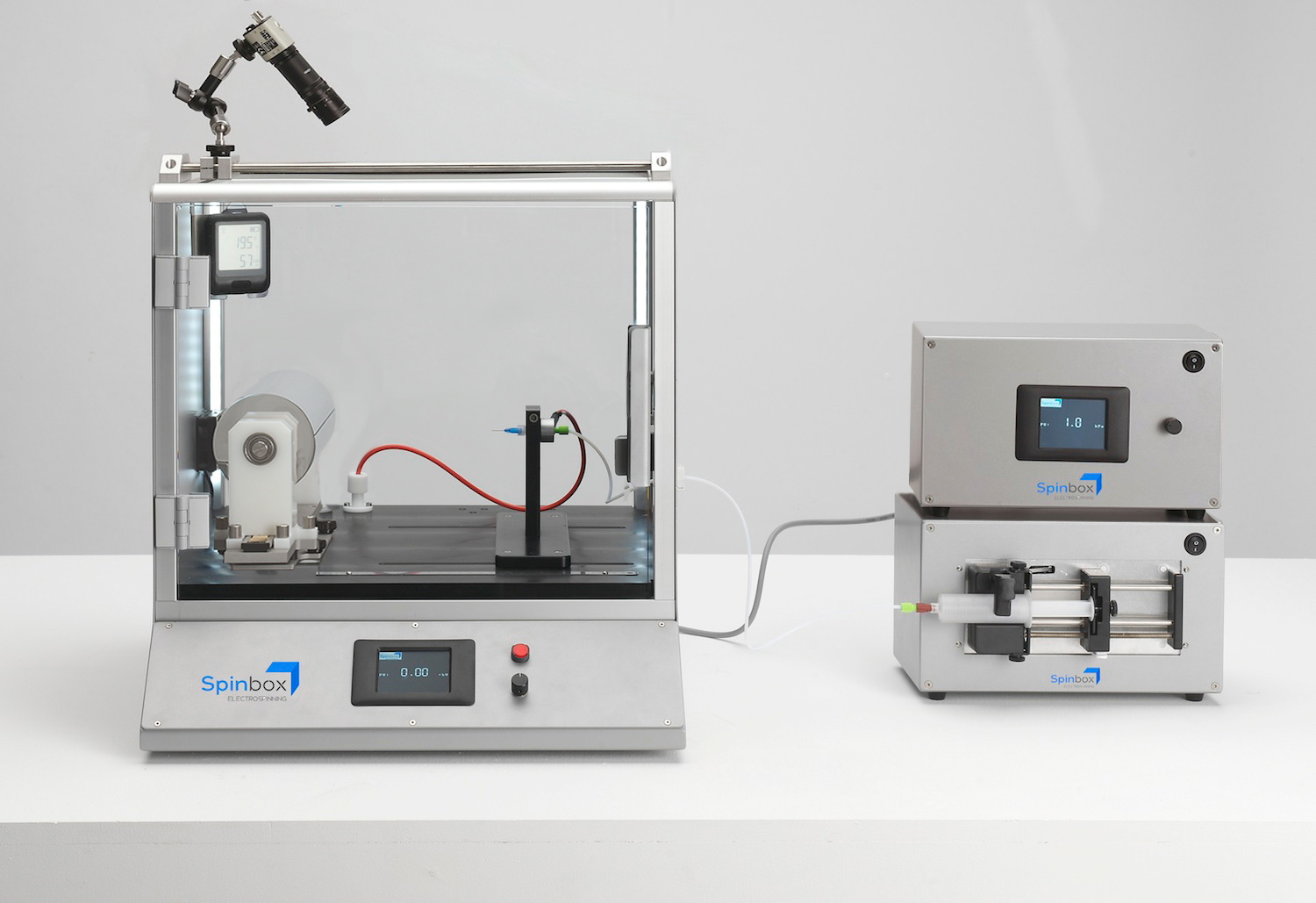
Advanced Spinbox Kit
Generate complex samples like core-shell and tubular structures with higher throughput and better homogeneity thanks to needle translation.
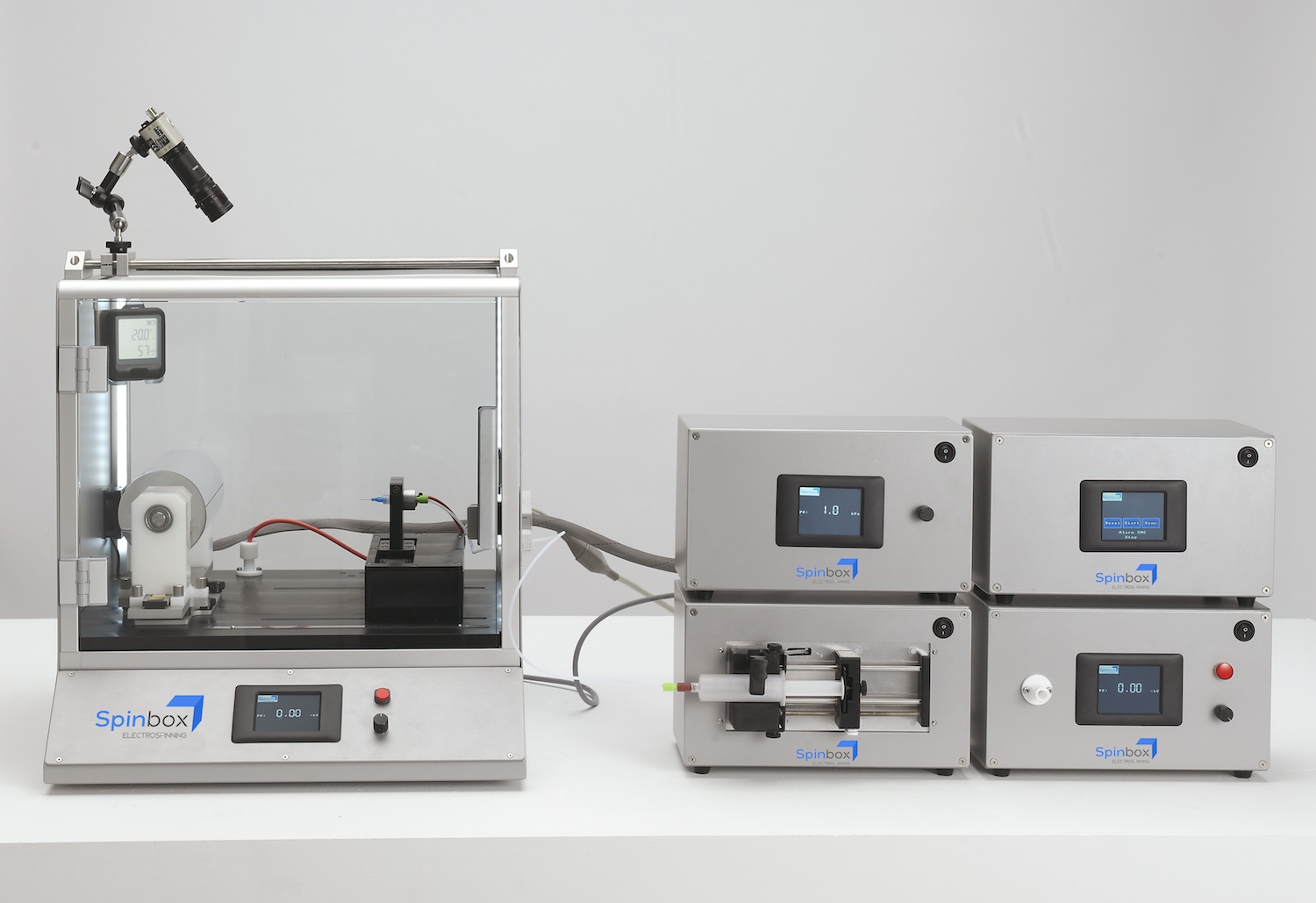
Spinbox®
Electrospinning & Electrospraying Applications
Biomedical & Tissue Engineering
Electrospun nanofibers are used to create scaffolds for tissue engineering applications. These scaffolds mimic the extracellular matrix, providing a supportive environment for cell growth and tissue regeneration. They are prevalent in wound healing, bone regeneration, nerve regeneration, and more.
Medical Devices
Whether as coatings for prefabricated structures, active ingredient additives, or total device fabrication, medical devices implement electrospun nanofibers and particles for enhanced therapeutic effectiveness. These fibers and particles can allow for improved performance in mechanical properties, biological microenvironment control, cellular integration, and many more application-specific advantages.
Drug Delivery
Electrospun fibers and/or particles can be loaded with drugs or therapeutic agents and used as drug delivery systems. Precisely controlled electrospinning parameters allow the high surface area-to-volume ratio and tunable properties of nanomaterials providing controlled release of drugs, making them suitable for targeted and sustained drug delivery.
Functional & Bio Textiles
The enhanced performance of textiles by imparting properties such as water resistance, flame retardancy, and antimicrobial activity can be accomplished using electrospun materials. These fibers are used in lightweight protective clothing, wound dressings, and specialty textiles for various applications.
Filtration & Separation
Nanofibrous membranes produced by electrospinning are employed in filtration and separation processes due to their small pore size and high porosity. They are used in air filtration, water filtration, oil-water separation, and other environmental applications. This can be done using high-throughput electrospinning methods, such as needle-less electrospinning.
Batteries & Fuel Cells
Energy storage and conversion devices such as batteries, supercapacitors, and fuel cells utilize electrospun nanofibrous materials for improved performance of these devices due to their high surface area and electrical conductivity. Ease of particle incorporation, such as ceramic/inorganic nanoparticles, and homogeneity in electrospinning promotes the efficiency of the fibrous materials electroconductivity.
Cosmetics
Electrospun nanofibers can be used as carriers for active cosmetic ingredients such as vitamins, antioxidants, peptides, plant extracts, and more to provide targeted treatment for things like anti-aging, anti-scarring, UV protection, or moisturizing. These nanofibers provide a large surface area and controlled release properties, ensuring better penetration into the desired area and enhanced efficacy of the active ingredients.
Environmental Remediation
Electrospun nanofibrous materials are employed in environmental remediation applications such as wastewater treatment, oil spill cleanup, and air pollution control. They can effectively remove pollutants and contaminants from the environment due to their high surface area and adsorption capacity.
Food Packaging
Electrospinning in food packaging involves utilizing nanofibers and incorporated particles to create innovative packaging materials with enhanced barrier properties against oxygen, moisture, and microbes, extending the shelf life and freshness of food products. These nanofibrous packaging materials offer a sustainable and environmentally friendly alternative to traditional packaging materials, contributing to the reduction of food waste and environmental impact in the food industry.
Spinbox®
Product Knowledgebase
Webinar
Advancements in Electrospun Scaffolds: Transitioning from 1D/2D Sheets to 3D Structures
Electrospinning has emerged as a leading platform for generating nanofibrous materials who…
Blog
Enhancing Efficacy of Bipolar Membranes through Electrospinning
Electrospinning has emerged as a transformative technique for fabricating fibrous material…
White Paper
Controlling the Orientation of Electrospun Nanofibers for Tissue Engineering
Electrospinning is a versatile and promising technique for fabricating nanofibrous scaffol…