Electrospinning & Electrospraying System
Fluidnatek® LE-500
The LE-500 is a robust system that allows researchers to produce pre-production volumes of production-quality electrospun fibers and/or electrosprayed particles. It offers advanced features, flexible configurations, and precise control for scientists and engineers working on advanced development projects, beta-release, and pre-market introduction activities.
Full Environmental Control
Pilot-scale
Production
Produce pilot-scale quantities of electrospun or electrosprayed materials with up to 8 liters of solution and 370 needles
Maximize
Production
Horizontal, vertical, and angled sample processing enables high throughput and fabrication of complex structures
Needle-based or Needle-less
Talk to an Instrumentation Specialist Today!
Advanced Electrospinning System for Pilot-Scale Production and Research
The Fluidnatek LE-500 is a robust and versatile electrospinning and electrospraying system, designed to bridge the gap between research and industrial-scale production. With the ability to handle batch volumes ranging from less than 1 mL to 8 L, it is ideal for scalable development of nanofibers and particles for applications in medical, pharmaceutical, and advanced materials industries. Equipped with a user-friendly touch-screen interface, dual high-voltage power supplies, and automated environmental controls, the LE-500 provides precise global control over process parameters and ensures reproducibility. Its modular design accommodates multiple emitters and collectors, including roll-to-roll systems and advanced rotating platforms, enabling the fabrication of uniform coatings, membranes, and composite structures. Engineered for safety and cleanroom compatibility, the LE-500 incorporates features like solvent vapor extraction, HEPA filtration, and UV-C sterilization. Whether for R&D or manufacturing, this system sets the standard for innovation and reliability in electrospinning technology.
Application Areas:
Fluidnatek LE-500
Product Features
High-Volume Processing
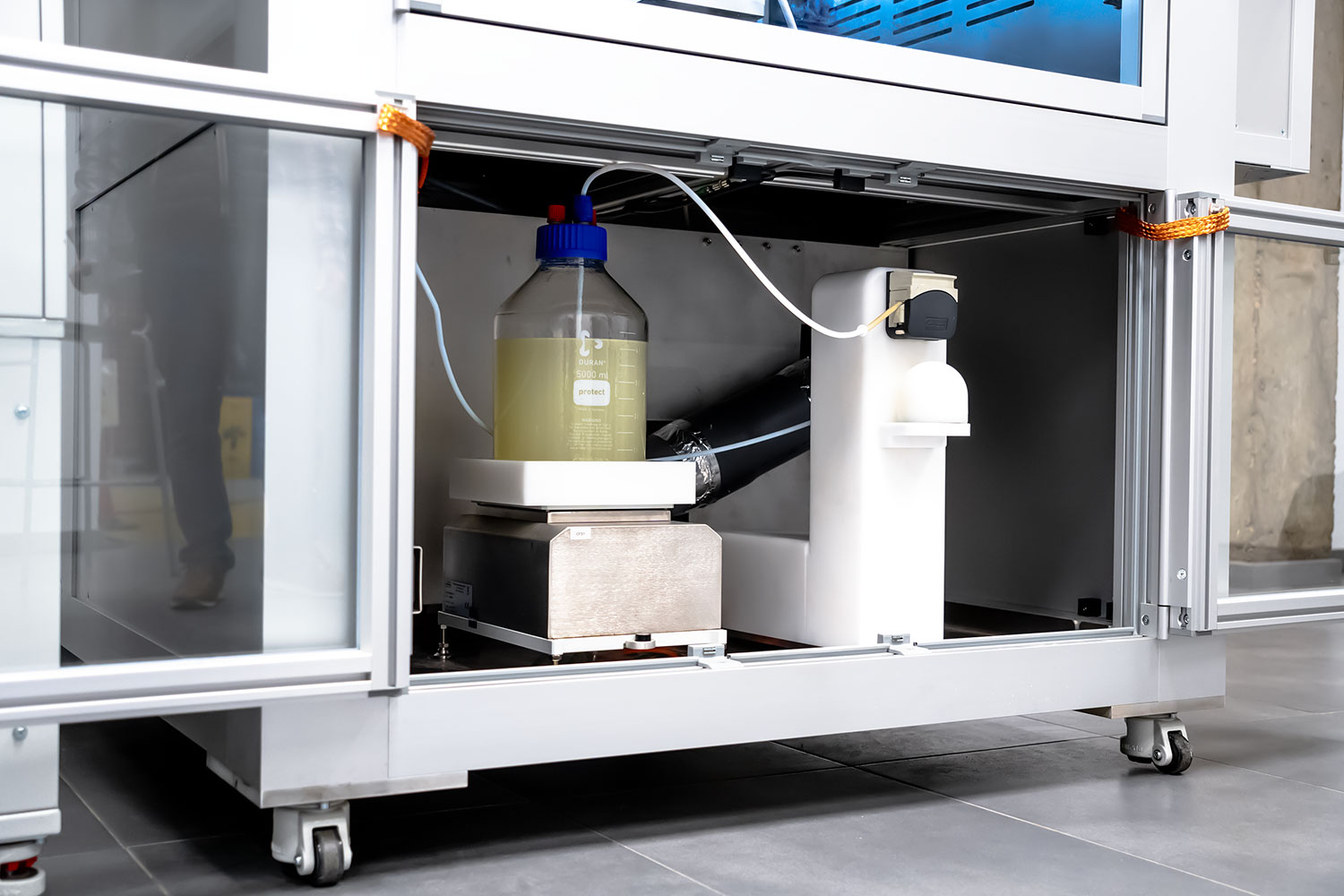
Scalable Multi-Emitter Configuration
Supporting up to 370 emitters, the LE-500 allows for high-throughput production of electrospun samples. The LE-500 is compatible with various emitter types, including single-phase and coaxial configurations, enabling users to tailor the setup to their application and scale-up needs. The multi-emitter design of the LE-500 has been engineered to maximize sample homogeneity during deposition, a critical advantage over competitor systems. Other features like field deflectors help ensure uniform deposition across the collection substrate producing consistent, high-quality results.
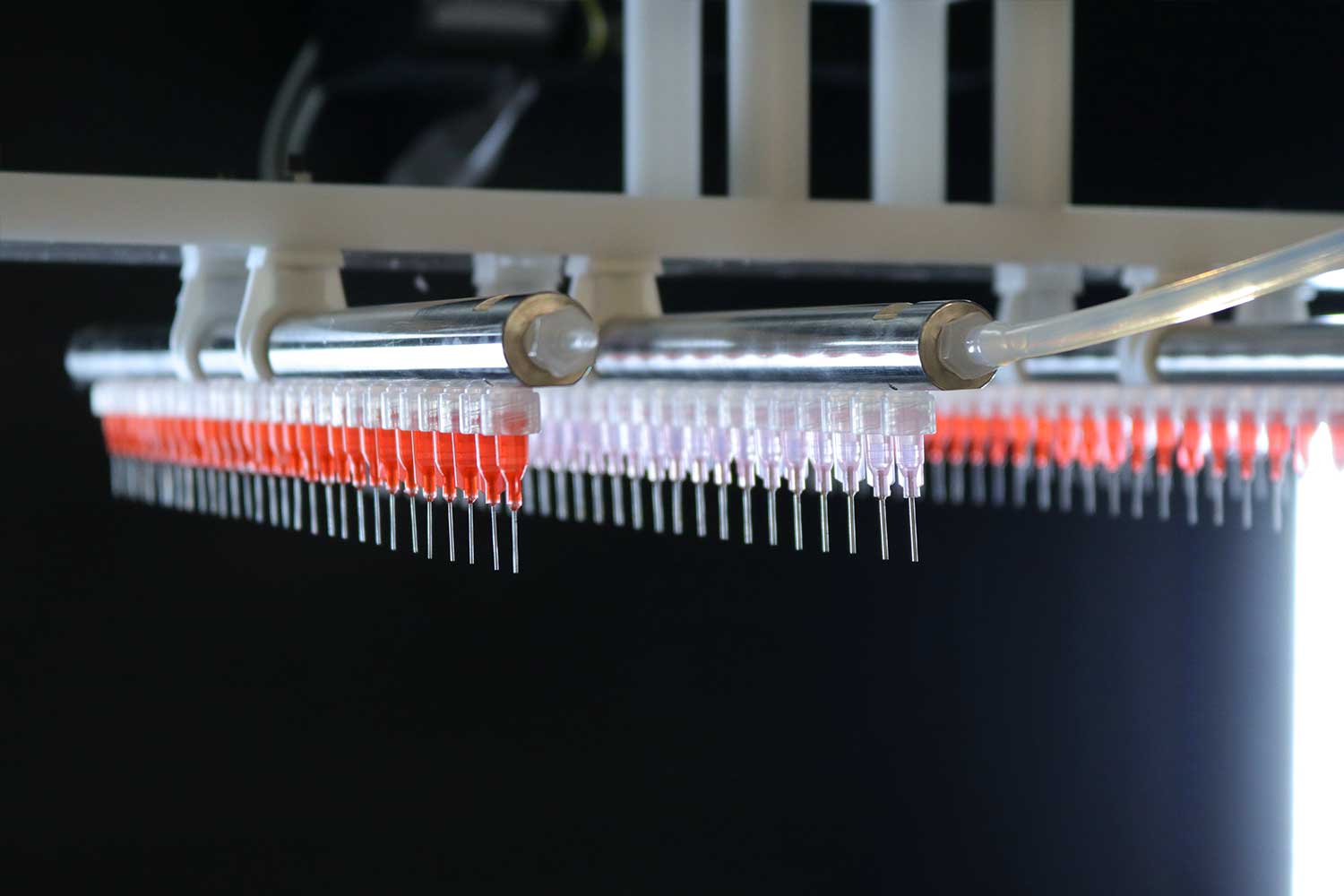
Precision Environmental Control
Offers precise environmental control with an optional Environmental Control Unit (ECU) to regulate temperature (18 – 45 °C), relative humidity (10 – 80%), and absolute humidity (6 – 16 g/kg) ensuring reproducibility and stability in fiber and particle morphology across batches. The conditioned air is HEPA filtered before entering the chamber, with airflow ranging from 90 to 180 m³/h.
Advanced Collection Systems
Includes multiple plug & play collection options such as flat plate, drum, mandrel, yarn, and roll-to-roll collectors, allowing flexibility to meet a diverse range of application requirements and enhance material consistency.
Enhanced Safety Features
The LE-500 features an actively regulated exhaust system that removes solvent vapors, prevents accumulation, and ensures operator safety, with interlocked doors and differential pressure control for added protection. Designed with operator safety in mind, the system adherers to stringent EU Directives (2006/42/EC, 2004/108/EC, 2006/95/EC) to protect users from high-voltage electrical discharges. It also includes a door-opening safety feature that activates the exhaust system at full speed to remove solvent vapors before the chamber door can be opened, ensuring safer conditions for the user.
Automated Controls & Diagnostics
Equipped with a touchscreen interface and intuitive software for real-time monitoring and precise control of process parameters, complemented by Ethernet connectivity for remote diagnostics and software updates. The software also supports the creation and storage of pre-set recipes, allowing users to save and load optimized parameter setups for consistent, repeatable processes. This functionality includes programmable multi-step recipes for advanced automation and workflow efficiency.
Data & Recipe Management
The system’s software supports recipe creation, data logging, and multi-user access. These capabilities ensure consistent reproducibility for every batch, allowing for precise control and documentation of processing conditions.
Motion and Positioning
Automated adjustments for emitter-to-collector distance and emitter motion ensure precise fiber and/or particle deposition. Unlike competitor systems that rely on moving the collector, the LE-500 moves the needle itself, allowing for finer control and more precise coating of substrates and devices. Low and high translational speed allow the user to optimize sample production to meet required homogeneity standards, ensure reproducibility, batch-to-batch consistency, and ease up process validation.
Versatile Solution Feeding
Offers versatile solution delivery options, including syringe pumps, peristaltic feeding with gravimetric control systems, and pressurized systems. Three types of syringe pumps are available to suit different needs: standard single-channel pumps for small-scale R&D, high-pressure twin-channel pumps for precise dual-solution delivery, and high-pressure four-channel pumps for larger volumes and solutions with high viscosity. The peristaltic pump with a gravimetric system is the ideal solution feeding system for increased throughput processes with flow rate above 50 L/h.
Modular & Upgradeable Design
Designed with modularity in mind, the LE-500 allows for on-demand upgrades to expand its functionality. These include a secondary spinning stage for processing two solutions with independent voltages for creating advanced structures, slit injectors for needleless processing, rotating collectors, and Taylor cone visualization systems. Additionally, it offers an in-line area density metrology system for real-time measurement and monitoring of deposition uniformity during roll-to-roll processing. This area density measurement feature is exclusively available on the LE-500.
Process Validation
The LE-500 can be provided with qualification documentation to support validation compliance, including Factory Acceptance Testing (FAT), Site Acceptance Testing (SAT), Installation Qualification (IQ), and Operational Qualification (OQ). These documents facilitate process validation and comply with standards such as Good Manufacturing Processes (GMP), Good Laboratory Practices (GLP), and Good Automated Manufacturing Practices (GAMP), meeting Food and Drug Administration (FDA) and International Organization for Standardization (ISO) requirements.
Fluidnatek LE-500
Product Accessories
Environmental Control Unit (ECU)
The optional Environmental Control Unit ensures tight control of environmental conditions by regulating temperature (18 – 45 °C) and relative humidity (10 – 80%), with stability ranges of ±1°C and ±3%. This feature enables reproducibility in fiber and particle morphology, making it ideal for advanced applications that require stable environmental conditions. The ECU is the ultimate accessory for batch-to-batch consistency all year round.
The LE-500 can also be modified to incorporate an open-loop nitrogen environment, reducing oxygen concentration by introducing a continuous nitrogen supply. This feature is particularly beneficial when working with flammable or explosive solvents, as it enhances operational safety by minimizing the risk of combustion. The system automatically disables processing if the oxygen concentration exceeds a user-defined safety limit, ensuring a controlled and safe environment during sensitive electrospinning processes.
High Definition Process Data Hub (HDPDH)
The optional HDPDH provides real-time updates, monitoring, and control of the electrospinning unit with 20+ viewable process parameters. This powerful, unique Industry 4.0 software tool provides a detailed record of process stability over time. The Process Data Hub ensures process consistency and repeatability between batches and across platforms, providing smooth scalability to higher throughput.
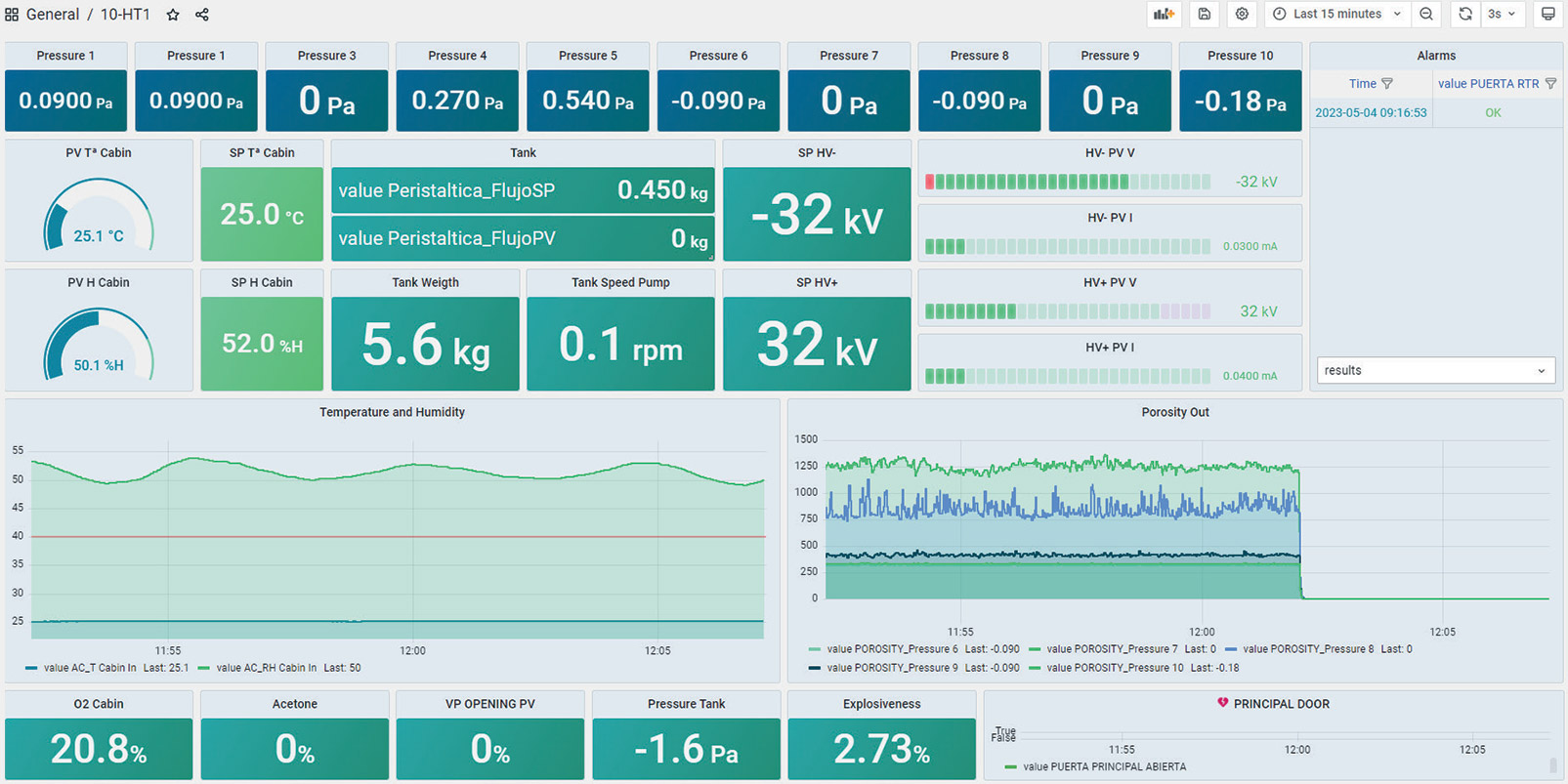
High-Voltage Options
The LE-500 includes dual high-voltage power supplies for emitters and collectors, capable of generating up to ±30 kV, with an optional upgrade to +50 kV for enhanced throughput and stability in demanding applications. Bipolar high voltages provide more production flexibility to chemically and physically manipulate the sample for the most demanding applications. These capabilities provide precision control for a wide range of materials, enabling the development of complex nanostructures.
Emitters
A variety of emitters are available, including single-phase, coaxial, and triaxial configurations, as well as others tailored for specific applications like bipolar or multi-layered samples. The system supports up to 370 emitters in multi-emitter configurations for high-throughput production, gas-assisted processing, and it offers needleless slit injectors, capable of generating multiple jets along their length, for significantly increased production capacity. These options provide flexibility for producing complex nanostructures and scaling up manufacturing processes. Optional accessories like the gas-assisted electrospinning modules increase throughput and process stability. A solvent gas jacket system prevents tip drying for volatile solutions.
Collectors
The system supports multiple plug & play collectors, such as flat plates, rotating drums, mandrels, and disk collectors. These options enable the creation of randomly oriented or aligned fibers, tubular structures, and large samples. For high-throughput production, collectors like roll-to-roll systems with conveyor belts are used to gather meters of material efficiently. Continuous yarns, composed of the same or multiple materials, can be collected using the electrospun fiber-yarn collection module.
Solution Feeding Systems
The LE-500 offers advanced feeding systems for different application needs including syringe pumps, pressurized reservoirs, peristaltic feeding with gravimetric control systems, and high-pressure syringe pumps for high-viscosity solutions. These systems provide precise control for both R&D and production-scale operations.
Metrology System
The optional in-line area density metrology system provides real-time measurement and monitoring of deposition uniformity during roll-to-roll processing.
Fluidnatek LE-500
Electrospinning & Electrospraying Applications
Biomedical & Tissue Engineering
Electrospun nanofibers are used to create scaffolds for tissue engineering applications. These scaffolds mimic the extracellular matrix, providing a supportive environment for cell growth and tissue regeneration. They are prevalent in wound healing, bone regeneration, nerve regeneration, and more.
Medical Devices
Whether as coatings for prefabricated structures, active ingredient additives, or total device fabrication, medical devices implement electrospun nanofibers and particles for enhanced therapeutic effectiveness. These fibers and particles can allow for improved performance in mechanical properties, biological microenvironment control, cellular integration, and many more application-specific advantages.
Drug Delivery
Electrospun fibers and/or particles can be loaded with drugs or therapeutic agents and used as drug delivery systems. Precisely controlled electrospinning parameters allow the high surface area-to-volume ratio and tunable properties of nanomaterials providing controlled release of drugs, making them suitable for targeted and sustained drug delivery.
Functional & Bio Textiles
The enhanced performance of textiles by imparting properties such as water resistance, flame retardancy, and antimicrobial activity can be accomplished using electrospun materials. These fibers are used in lightweight protective clothing, wound dressings, and specialty textiles for various applications.
Filtration & Separation
Nanofibrous membranes produced by electrospinning are employed in filtration and separation processes due to their small pore size and high porosity. They are used in air filtration, water filtration, oil-water separation, and other environmental applications. This can be done using high-throughput electrospinning methods, such as needle-less electrospinning.
Batteries & Fuel Cells
Energy storage and conversion devices such as batteries, supercapacitors, and fuel cells utilize electrospun nanofibrous materials for improved performance of these devices due to their high surface area and electrical conductivity. Ease of particle incorporation, such as ceramic/inorganic nanoparticles, and homogeneity in electrospinning promotes the efficiency of the fibrous materials electroconductivity.
Cosmetics
Electrospun nanofibers can be used as carriers for active cosmetic ingredients such as vitamins, antioxidants, peptides, plant extracts, and more to provide targeted treatment for things like anti-aging, anti-scarring, UV protection, or moisturizing. These nanofibers provide a large surface area and controlled release properties, ensuring better penetration into the desired area and enhanced efficacy of the active ingredients.
Environmental Remediation
Electrospun nanofibrous materials are employed in environmental remediation applications such as wastewater treatment, oil spill cleanup, and air pollution control. They can effectively remove pollutants and contaminants from the environment due to their high surface area and adsorption capacity.
Food Packaging
Electrospinning in food packaging involves utilizing nanofibers and incorporated particles to create innovative packaging materials with enhanced barrier properties against oxygen, moisture, and microbes, extending the shelf life and freshness of food products. These nanofibrous packaging materials offer a sustainable and environmentally friendly alternative to traditional packaging materials, contributing to the reduction of food waste and environmental impact in the food industry.
Fluidnatek LE-500
Product Knowledgebase
Webinar
Advancements in Electrospun Scaffolds: Transitioning from 1D/2D Sheets to 3D Structures
Electrospinning has emerged as a leading platform for generating nanofibrous materials who…
Blog
Fabricating Complex Geometries with Electrospinning
Electrospinning has emerged as a transformative technique for fabricating fibrous material…
White Paper
Controlling the Orientation of Electrospun Nanofibers for Tissue Engineering
Electrospinning is a versatile and promising technique for fabricating nanofibrous scaffol…